Numerical-field analysis of differential leakage reactance of stator winding in three-phase induction motors
DOI:
https://doi.org/10.20998/2074-272X.2025.2.02Keywords:
induction motor, three-phase stator winding, differential leakage reactance, classical design, numerical-field calculations, magnetic flux linkage, harmonic analysisAbstract
Introduction. The differential leakage reactance (DLR) of the stator winding of three-phase induction motors (TIM) is considered. It is known that DLR is the sum of the self-induction resistances of the winding from all harmonics of its magnetic field, excluding the first one, and its analytical definition is too complicated. But this reactance is a mandatory design element, including for calculating a number of other parameters and characteristics of such motors. Problem. Because of this, in the current classical design methods, the DLR are determined by a simplified formula with the addition of a number of coefficients, tabular and graphical dependencies. As a result, not only the physical and mathematical meaning of DLR is lost, but even the accuracy of its calculation is difficult to assess. Goal. The purpose of the paper consists in the comparative verification of the classical design calculation of the DLR of the TIM stator winding by numerical-field analysis of the harmonic composition of the EMF of self-inductions in this winding and by the determination of the considered DLR on such a basis. Methodology. Harmonic analysis is performed by obtaining the angular and time discrete functions of the magnetic flux linkage (MFL) of the stator winding with their formation in two ways: single-position calculation of the magnetic field and conditional rotation of the phase zones of the winding, or multi-position calculations of the rotating magnetic field and determination of the MFL of stationary phase zones. Results. Computational analysis is performed for nine common variants of TIM, designed according to a single classical method with variation of their power and the number of poles. Originality. A comparison of the results of the classical and numerical-field calculations of the DLR using the FEMM program showed their large discrepancy, which is attributed to the indicated inadequacy of the first one, since the second option is devoid of the shortcomings of the first one due to the fact that it takes into account the dimensions of the TIM structures, the saturation of the magnetic circuit and the physical and mathematical essence of the parameters and values under consideration. Practical value. The presented method of numerical-field analysis and the obtained results of calculating the DLR of the TIM stator winding are recommended as a basis for improving the system of their design. At the same time, a similar approach can be applied to the DLR of the TIM rotor winding, but taking into account its features. References 27, tables 13, figures 7.
References
Goldberg O.D., Gurin Ya.S., Sviridenko I.S. Design of electrical machines. 2nd ed., revised and additional. Moscow, Higher School Publ., 2001. 430 p. (Rus).
Kopylov I.P., Goryainov F.A., Klokov B.K. Electrical machines designing. Moscow, Yurait Publ., 2011. 767 p. (Rus).
Udomsuk S., Areerak K., Areerak T., Areerak K. Online Estimation of Three-Phase Induction Motor Parameters Using an Extended Kalman Filter for Energy Saving. Energies, 2024, vol. 17, no. 9, art. no. 2115, pp. 1-17. doi: https://doi.org/10.3390/en17092115.
Aib A., Khodja D.E., Chakroune S., Rahali H. Fuzzy current analysis-based fault diagnostic of induction motor using hardware co-simulation with field programmable gate array. Electrical Engineering & Electromechanics, 2023, no. 6, pp. 3-9. doi: https://doi.org/10.20998/2074-272X.2023.6.01.
Abu Ibaid O.Z.I., Belhamdi S., Abid M., Chakroune S., Mouassa S., Al-Sagar Z.S. Wavelet packet analysis for rotor bar breakage in an inverter induction motor. Electrical Engineering & Electromechanics, 2023, no. 3, pp. 3-11. doi: https://doi.org/10.20998/2074-272X.2023.3.01.
Sakhara S., Brahimi M., Nacib L., Layadi T.M. Application of a wavelet neural network approach to detect stator winding short circuits in asynchronous machines. Electrical Engineering & Electromechanics, 2023, no. 3, pp. 21-27. doi: https://doi.org/10.20998/2074-272X.2023.3.03.
Popovych O.M., Golovan I.V. Modeling of induction motors in electromechanical systems considering stator iron losses. Technical Electrodynamics, 2024, no. 5, pp. 24-29. (Ukr). doi: https://doi.org/10.15407/techned2024.05.024.
Tumbek M., Oner Y., Kesler S. Optimal design of induction motor with multi-parameter by FEM method. 2015 9th International Conference on Electrical and Electronics Engineering (ELECO), 2015, pр. 1053-1056. doi: https://doi.org/10.1109/ELECO.2015.7394483.
Popovych O.M., Golovan І.V. Complex design tools for improvement of electromechanical systems with induction motors. Technical Electrodynamics, 2022, no. 2, pp. 52-59. doi: https://doi.org/10.15407/techned2022.02.052.
Peresada S.M., Nikonenko Y.O., Kovbasa S.M., Kuznietsov O. Flux observer adaptive to induction motors active rotor resistance variations. Technical Electrodynamics, 2022, no. 5, pp. 45-51. (Ukr). doi: https://doi.org/10.15407/techned2022.05.045.
Milykh V.I. Numerical-field analysis of active and reactive winding parameters and mechanical characteristics of a squirrel-cage induction motor. Electrical Engineering & Electromechanics, 2023, no. 4, pp. 3-13. doi: https://doi.org/10.20998/2074-272X.2023.4.01.
Milykh V. Numerical-field analysis of the magnetic conductivity of the slot dispersion of the stator winding of induction motors. Bulletin of NTU «KhPI». Series: Problems of electrical machines and apparatus perfection. Theory and practice, 2023, no. 2 (10), pp. 13-19. (Ukr). doi: https://doi.org/10.20998/2079-3944.2023.2.03.
Diarra M.N., Li Y., Zhao X. Induction Motors Parameters Identification by Starting Process Using Quantum Particle Swarm Optimization-Trust Region Algorithm (QPSO-TRA). 2023 International Conference on Applied Intelligence and Sustainable Computing (ICAISC), 2023, pp. 1-6. doi: https://doi.org/10.1109/ICAISC58445.2023.10200090.
Rajput S., Bender E., Averbukh M. Simplified algorithm for assessment equivalent circuit parameters of induction motors. IET Electric Power Applications, 2020, vol. 14, no. 3, pp. 426-432. doi: https://doi.org/10.1049/iet-epa.2019.0822.
Lee K., Frank S., Sen P.K., Polese L.G., Alahmad M., Waters C. Estimation of induction motor equivalent circuit parameters from nameplate data. 2012 North American Power Symposium (NAPS), 2012, pp. 1-6. doi: https://doi.org/10.1109/NAPS.2012.6336384.
Gülbahçe M.O., Karaaslan M.E. Estimation of induction motor equivalent circuit parameters from manufacturer’s datasheet by particle swarm optimization algorithm for variable frequency drives. Electrica, 2022, vol. 22, no. 1, pp. 16-26. doi: https://doi.org/10.5152/electrica.2021.21122.
Mölsä E., Tiitinen L., Saarakkala S., Peretti L., Hinkkanen M. Standstill Self-Commissioning of an Induction Motor Drive. 2020 IEEE Energy Conversion Congress and Exposition (ECCE), 2020, pp. 3044-3050. doi: https://doi.org/10.1109/ECCE44975.2020.9236035.
Chen H., Bi C. An effective method for determination and characteristic analysis of induction motor parameters. IET Electric Power Applications, 2022, vol. 16, no. 5, pp. 605-615. doi: https://doi.org/10.1049/elp2.12180.
Caruso M., Tommaso A.O.D., Giangrasso L., Marignetti F., Miceli R., Rizzo R. Differential Leakage Factor in Electrical Machines Equipped with Asymmetrical Multiphase Windings: a General Investigation. 2019 Fourteenth International Conference on Ecological Vehicles and Renewable Energies (EVER), 2019, pp. 1-7. doi: https://doi.org/10.1109/EVER.2019.8813617.
Di Tommaso A.O., Genduso F., Miceli R., Ricco Galluzzo G. An Exact Method for the Determination of Differential Leakage Factors in Electrical Machines With Non-Symmetrical Windings. IEEE Transactions on Magnetics, 2016, vol. 52, no. 9, pp. 1-9. doi: https://doi.org/10.1109/TMAG.2016.2562602.
Guedes J.J., Castoldi M.F., Goedtel A., Agulhari C.M., Sanches D.S. Parameters estimation of three-phase induction motors using differential evolution. Electric Power Systems Research, 2018, vol. 154, pp. 204-212. doi: https://doi.org/10.1016/j.epsr.2017.08.033.
Slobozhansky Electromechanical Plant «SLEMZ». Available at: https://slemz.com.ua (Accessed: 26 August 2024).
DNEPRORESURS LLC. Available at: https://elmo.ua/uk (Accessed: 26 August 2024).
Finite Element Method Magnetics: Download – Stable Distribution (21Apr2019) – 64-bit Executable. Available at: https://www.femm.info/wiki/Download (Accessed: 22 July 2024).
Milykh V.I. Numerical-field analysis of temporal functions and harmonic composition of EMF in windings of a three-phase asynchronous motor. Technical Electrodynamics. 2018, no. 3, pp. 56-65. (Rus). doi: https://doi.org/10.15407/techned2018.03.056.
Milykh V.I. The system of automated formation of electrical machines computational models for the FEMM software environment. Technical Electrodynamics. 2018, no. 4, pp. 74-78. (Ukr). doi: https://doi.org/10.15407/techned2018.04.074.
Milykh V.I., Polyakova N.V. Harmonious analysis of electromagnetic sizes three-phase winding of stators of turbogenerator on basis classic and numeral field methods. Technical Electrodynamics, 2013, no. 3, pp. 40-49. (Rus).
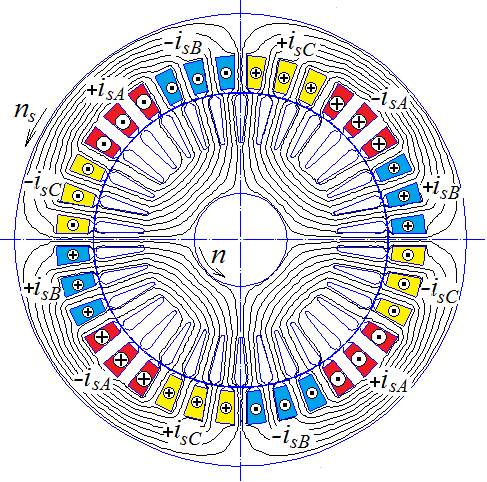
Downloads
Published
How to Cite
Issue
Section
License
Copyright (c) 2025 V. I. Milykh

This work is licensed under a Creative Commons Attribution-NonCommercial 4.0 International License.
Authors who publish with this journal agree to the following terms:
1. Authors retain copyright and grant the journal right of first publication with the work simultaneously licensed under a Creative Commons Attribution License that allows others to share the work with an acknowledgement of the work's authorship and initial publication in this journal.
2. Authors are able to enter into separate, additional contractual arrangements for the non-exclusive distribution of the journal's published version of the work (e.g., post it to an institutional repository or publish it in a book), with an acknowledgement of its initial publication in this journal.
3. Authors are permitted and encouraged to post their work online (e.g., in institutional repositories or on their website) prior to and during the submission process, as it can lead to productive exchanges, as well as earlier and greater citation of published work.