Increasing the damping properties of the magnetorheological actuator of the vehicle suspension control system
DOI:
https://doi.org/10.20998/2074-272X.2024.5.11Keywords:
magnetic field, magnetorheological actuator, anisotropic magnetorheological elastomer, control system, vehicle suspension, dampingAbstract
Introduction. In accordance with one of the ways of solving the problem of increasing the smoothness of the vehicles, a controlled suspension is proposed, which is created on the basis of the use of «smart» materials – magnetorheological elastomers, the mechanical properties of which, in particular, damping, can be changed with the help of a controlling magnetic field. This is implemented with the help of the magnetorheological actuator of the suspension control system, which has the form of an elastic bushing of the suspension arm, consisting of several electrically connected in series toroid-like coils (with a core of magnetorheological elastomer). The device is powered by current, the value of which is controlled by the operator, or automatically, depending on the road profile and driving mode. Magnetorheological actuators (elastic bushings) are placed in the holes of the suspension levers instead of standard rubber ones and combined with a controlled current source. Thus, the suspension becomes controllable, which makes it possible to set the necessary vibration damping of the vehicle body to increase its smoothness. Problem. The disadvantage of the previous designs of the magnetorheological actuator is the insufficient amount of the magnetic flux density and the unevenness of its distribution within the elastic bushings. As a result, the damping properties of such controlled suspensions become insufficiently effective, which reduces the possibility of increasing the smoothness of the vehicles. The purpose of the work is to increase the damping properties of the magnetorheological actuator of the vehicle suspension control system, which will increase the control efficiency. The task is to improve the design of the performing magnetorheological device, to carry out calculations and develop a calculation scheme of the study, to determine the average magnetic flux density value and its distribution across the cross-section of the device, to calculate the dependence of the device damping indicator on the magnetic flux density, to compare the damping indicators of the improved device with previously known ones. Methodology. Research tasks were solved on the basis of magnetic field analysis using methods of magnetic field theory and SOLIDWORKS® and FEMM software packages, as well as analysis of the dependence of the damping properties of bushings from magnetorheological elastomers on magnetic flux density. A description of the design and principle of operation of the magnetorheological actuator of the vehicle suspension characteristics control system is given, based on which the calculation scheme was developed. Results. The results of research calculations showed that the average value of magnetic flux density in the proposed design of the device reached 0.85 T, its distribution became fairly uniform, and there were no zones where it was abnormally small. For the first time, the dependence of the damping index on the magnetic flux density of the controlling magnetic field has signs of scientific novelty. It was found that this indicator for the proposed design of the device increased by 22 % compared to previous other designs, which will increase the efficiency of the control system and the smoothness of the vehicle. A positive result was achieved due to the following features of the proposed design of the suspension actuator: the elastic sleeve consists of several coaxially located actuators made of anisotropic magnetorheological elastomer, in which the conglomerates of the ferromagnetic filler during the manufacturing process are located collinear to the direction of the angular deformations of the sleeve and the control magnetic field flux density vector, and the devices have control coils located on their surfaces, which are made of conductive elastic elastomer and electrically connected in a series circuit. Originality. The control method, previous designs and construction of this controlled suspension are protected by patents of Ukraine. Practical value. The direction of further research is to optimize the parameters of the control coils in order to reduce the energy consumption for them and to protect them from overheating. References 20, figures 10.
References
Dushchenko V.V., Masliev A.O. Use of materials intelligent systems at the nodes cushioning prospective military tracked and wheeled vehicles. Military Technical Collection, 2016, no. 14, pp. 7-13. (Ukr). doi: https://doi.org/10.33577/2312-4458.14.2016.7-13.
Zou Z., Zhang H., Liao C., Wang N., Choi S.-B. Hydrodynamic behaviors of settled magnetorheological fluid redispersion under active dispersing mechanism: simulation and experiment. Smart Materials and Structures, 2022, vol. 31, no. 9, art. no. 097001. doi: https://doi.org/10.1088/1361-665X/ac86b0.
Deng L., Sun S., Jin S., Li Z., Du H., Zhang S., Li W. Development of a new magnetorheological impact damper with low velocity sensitivity. Smart Materials and Structures, 2022, vol. 31, no. 9, art. no. 095042. doi: https://doi.org/10.1088/1361-665X/ac864d.
Zhang J., Qiao Y., Zhang M., Zhai P. Magnetorheological behavior of isotropic silicone rubber-based magnetorheological elastomers under coupled static–dynamic compressive loads. Smart Materials and Structures, 2022, vol. 31, no. 9, art. no. 095010. doi: https://doi.org/10.1088/1361-665X/ac7d24.
Erenchun A., Prieto B., Artetxe G., Gil-Negrete N. Practical design of an electromagnet for the compression characterization of magnetorheological elastomers. Smart Materials and Structures, 2022, vol. 31, no. 9, art. no. 095005. doi: https://doi.org/10.1088/1361-665X/ac7bbe.
Ahamed R., Choi S.-B., Ferdaus M.M. A state of art on magneto-rheological materials and their potential applications. Journal of Intelligent Material Systems and Structures, 2018, vol. 29, no. 10, pp. 2051-2095. doi: https://doi.org/10.1177/1045389X18754350.
Bastola A.K., Paudel M., Li L. Magnetic circuit analysis to obtain the magnetic permeability of magnetorheological elastomers. Journal of Intelligent Material Systems and Structures, 2018, vol. 29, no. 14, pp. 2946-2953. doi: https://doi.org/10.1177/1045389X18781046.
Behrooz M., Wang X., Gordaninejad F. Performance of a new magnetorheological elastomer isolation system. Smart Materials and Structures, 2014, vol. 23, no. 4, art. no. 045014. doi: https://doi.org/10.1088/0964-1726/23/4/045014.
Dargahi A., Sedaghati R., Rakheja S. On the properties of magnetorheological elastomers in shear mode: Design, fabrication and characterization. Composites Part B: Engineering, 2019, vol. 159, pp. 269-283. doi: https://doi.org/10.1016/j.compositesb.2018.09.080.
Krautz M., Werner D., Schrödner M., Funk A., Jantz A., Popp J., Eckert J., Waske A. Hysteretic behavior of soft magnetic elastomer composites. Journal of Magnetism and Magnetic Materials, 2017, vol. 426, pp. 60-63. doi: https://doi.org/10.1016/j.jmmm.2016.11.048.
Agirre-Olabide I., Kuzhir P., Elejabarrieta M.J. Linear magneto-viscoelastic model based on magnetic permeability components for anisotropic magnetorheological elastomers. Journal of Magnetism and Magnetic Materials, 2018, vol. 446, pp. 155-161. doi: https://doi.org/10.1016/j.jmmm.2017.09.017.
Vasco V.M., Grebenuyk S.M., Reshevskaya E.S. A determination of stress-strain state of elastomeric isolator. Bulletin of Zaporizhzhіa National University. Physical & Mathematical Sciences, 2015, no. 3, pp. 36-41. (Rus).
Wang Q., Dong X., Li L., Ou J. Study on an improved variable stiffness tuned mass damper based on conical magnetorheological elastomer isolators. Smart Materials and Structures, 2017, vol. 26, no. 10, art. no. 105028. doi: https://doi.org/10.1088/1361-665X/aa81e8.
Erenchun A., Prieto B., Artetxe G., Gil-Negrete N. Practical design of an electromagnet for the compression characterization of magnetorheological elastomers. Smart Materials and Structures, 2022, vol. 31, no. 9, art. no. 095005. doi: https://doi.org/10.1088/1361-665X/ac7bbe.
Kawasetsu T., Horii T., Ishihara H., Asada M. Flexible Tri-Axis Tactile Sensor Using Spiral Inductor and Magnetorheological Elastomer. IEEE Sensors Journal, 2018, vol. 18, no. 14, pp. 5834-5841. doi: https://doi.org/10.1109/JSEN.2018.2844194.
Qi S., Guo H., Chen J., Fu J., Hu C., Yu M., Wang Z.L. Magnetorheological elastomers enabled high-sensitive self-powered tribo-sensor for magnetic field detection. Nanoscale, 2018, vol. 10, no. 10, pp. 4745-4752. doi: https://doi.org/10.1039/C7NR09129J.
Sun S., Yang J., Yildirim T., Du H., Alici G., Zhang S., Li W. Development of a nonlinear adaptive absorber based on magnetorheological elastomer. Journal of Intelligent Material Systems and Structures, 2018, vol. 29, no. 2, pp. 194-204. doi: https://doi.org/10.1177/1045389X17733053.
Dushchenko V.V., Maslіev V.G., Nanivskyi R.A., Maslіev A.O. Application of magnetorheological elastomers for performance control of cushioning systems for wheeled vehicles. Electrical Engineering & Electromechanics, 2019, no. 5, pp. 50-59. doi: https://doi.org/10.20998/2074-272X.2019.5.09.
Dushchenko V., Masliiev A. Suspension with adjustable stiffness and damping. Patent UA, no. 110476. 2016. (Ukr).
Dushchenko V., Masliiev A., Masliiev V. Adjustable vehicle suspension. Patent UA, no. 149223. 2021. (Ukr).
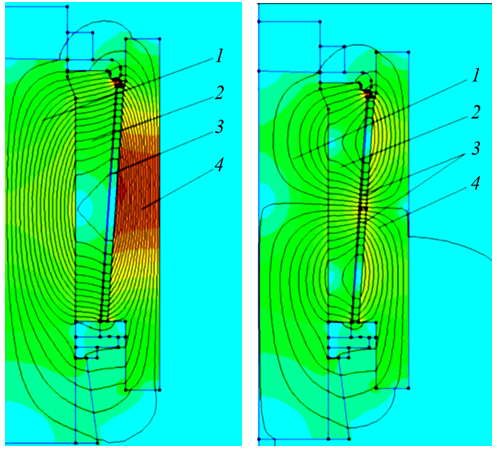
Downloads
Published
How to Cite
Issue
Section
License
Copyright (c) 2024 V. V. Dushchenko, A. O. Masliev, B. G. Liubarskyi, R. A. Nanivskyi, V. G. Masliev, O. M. Ahapov, D. I. Iakunin

This work is licensed under a Creative Commons Attribution-NonCommercial 4.0 International License.
Authors who publish with this journal agree to the following terms:
1. Authors retain copyright and grant the journal right of first publication with the work simultaneously licensed under a Creative Commons Attribution License that allows others to share the work with an acknowledgement of the work's authorship and initial publication in this journal.
2. Authors are able to enter into separate, additional contractual arrangements for the non-exclusive distribution of the journal's published version of the work (e.g., post it to an institutional repository or publish it in a book), with an acknowledgement of its initial publication in this journal.
3. Authors are permitted and encouraged to post their work online (e.g., in institutional repositories or on their website) prior to and during the submission process, as it can lead to productive exchanges, as well as earlier and greater citation of published work.