Computational studies of electromagnetic field propagation and deforming of structural elements for a thin-walled curved workpiece and an inductor
DOI:
https://doi.org/10.20998/2074-272X.2024.2.08Keywords:
computational analysis, electromagnetic field, electromagnetic forming, deformation, finite element methodAbstract
Introduction. At the present stage of industrial development, the electromagnetic field is widely used in various technological processes. The force effect of an electromagnetic field on conductive materials is used in a class of technological operations called electromagnetic forming. Problem. Under the conditions of electromagnetic forming, the main element of the technological equipment – the inductor – is simultaneously subjected to the force impact with the workpiece. At certain levels of the electromagnetic field, the deformation of the inductor becomes so significant that it can lead to a loss of its efficiency. Goal. Computational analysis of a thin-walled curved workpiece and a two-turn inductor under the conditions of electromagnetic processing of the workpiece corner zone. Determining the distribution of quantitative characteristics of the electromagnetic field and the stress-strain state and conducting assessments based on them regarding the efficiency of the technological operation. Methodology. Computational modeling using the finite element method as a method of numerical analysis. The results on the distribution of quantitative characteristics of the electromagnetic field and components of the stress-strain state for a thin-walled workpiece and an inductor are obtained. It is shown that for the specified characteristics of the technological operation, the inductor remains operational, and plastic deformations occur in the workpiece. A series of calculations were carried out, in which some parameters of the technological system were varied. Originality. For the first time, the results of the calculation analysis of the quantitative characteristics distribution of the electromagnetic field of the deformation process for the «inductor – thin-walled curved workpiece» system are presented. Practical value. The presented design scheme of a curved thin-walled workpiece and a two-turn inductor, the method of calculation analysis and some obtained results can be used in the analysis of electromagnetic processing of thin-walled structures that contain curved elements.
References
Psyk V., Risch D., Kinsey B.L., Tekkayaa A.E., Kleiner M. Electromagnetic forming – a review. Journal of Materials Processing Technology, 2011, vol. 211, no. 5, pp. 787-829. doi: https://doi.org/10.1016/j.jmatprotec.2010.12.012.
Gayakwad D., Dargar M.K., Sharma P.K., Purohit R., Rana R.S. A Review on Electromagnetic Forming Process. Procedia Materials Science, 2014, vol. 6, pp. 520-527. doi: https://doi.org/10.1016/j.mspro.2014.07.066.
Batygin Yu.V., Chaplygin E.A., Shinderuk S.A., Strelnikova V.A. The main inventions for technologies of the magnetic pulsed attraction of the sheet metals. A brief review. Electrical Engineering & Electromechanics, 2018, no. 3, pp. 43-52. doi: https://doi.org/10.20998/2074-272X.2018.3.06.
Batygin Y.V., Chaplygin E.A. Vortical currents in flat metallic sheet. Electrical Engineering & Electromechanics, 2006, no. 5, pp. 54-59. (Rus).
Batygin Yu., Barbashova M., Sabokar O. Electromagnetic Metal Forming for Advanced Processing Technologies. Cham, Springer International Publ. AG., 2018. 93 p. doi: https://doi.org/10.1007/978-3-319-74570-1.
Batygin Y.V., Golovashchenko S.F., Gnatov A.V., Smirnov D.O. Magnetic field and pressures excited by four pairwise coplanar solenoids in the cavity of a rectangular tube. Electrical Engineering & Electromechanics, 2010, no. 2, pp. 46-49. (Rus).
Batygin Y.V., Serikov G.S. Magnetic field and pressures excited by a single-turn inductor in a corner bend of a sheet worpiece. Electrical Engineering & Electromechanics, 2006, no. 6, pp. 66-70. (Rus).
Unger J., Stiemer M., Schwarze M., Svendsen B., Blum H., Reese S. Strategies for 3D simulation of electromagnetic forming processes. Journal of Materials Processing Technology, 2008, vol. 199, no. 1-3, pp. 341-362. doi: https://doi.org/10.1016/j.jmatprotec.2007.08.028.
Stiemer M., Unger J., Svendsen B., Blum H. An arbitrary Lagrangian Eulerian approach to the three-dimensional simulation of electromagnetic forming. Computer Methods in Applied Mechanics and Engineering, 2009, vol. 198, no. 17-20, pp. 1535-1547. doi: https://doi.org/10.1016/j.cma.2009.01.014.
Mamalis A.G., Manolakos D.E., Kladas A.G., Koumoutsos A.K. Electromagnetic Forming Tools and Processing Conditions: Numerical Simulation. Materials and Manufacturing Processes, 2006, vol. 21, no. 4, pp. 411-423. doi: https://doi.org/10.1080/10426910500411785.
Yu H., Chen J., Liu W., Yin H., Li C. Electromagnetic forming of aluminum circular tubes into square tubes: Experiment and numerical simulation. Journal of Manufacturing Processes, 2018, vol. 31, pp. 613-623. doi: https://doi.org/10.1016/j.jmapro.2017.12.019.
Doley J.K., Kore S.D. Fully Coupled Numerical Simulation of Electromagnetic Forming. Key Engineering Materials, 2012, vol. 504-506, pp. 1201-1206. doi: https://doi.org/10.4028/www.scientific.net/KEM.504-506.1201.
Altenbach H., Morachkovsky O., Naumenko K., Lavinsky D. Inelastic deformation of conductive bodies in electromagnetic fields. Continuum Mechanics and Thermodynamics, 2016, vol. 28, no. 5, pp. 1421-1433. doi: https://doi.org/10.1007/s00161-015-0484-8.
Lavinsky D.V. Analysis of elastic-plastic deformation when modeling the «corner filling» operation. Part 1. Bulletin of the National Technical University «KhPI» Series: Dynamics and Strength of Machines, 2010, no. 37, pp. 100-104. (Rus).
Lavinsky D.V., Zaitsev Yu.I. Computational analysis method of the electromagnetic field propagation and deformation of conductive bodies. Electrical Engineering & Electromechanics, 2023, no. 5, pp. 77-82. doi: https://doi.org/10.20998/2074-272X.2023.5.11.
Lavinskii D.V., Morachkovskii O. K. Elastoplastic Deformation of Bodies Interacting Through Contact Under the Action of Pulsed Electromagnetic Field. Strength of Materials, 2016, vol. 48, no. 6, pp. 760-767. doi: https://doi.org/10.1007/s11223-017-9822-3.
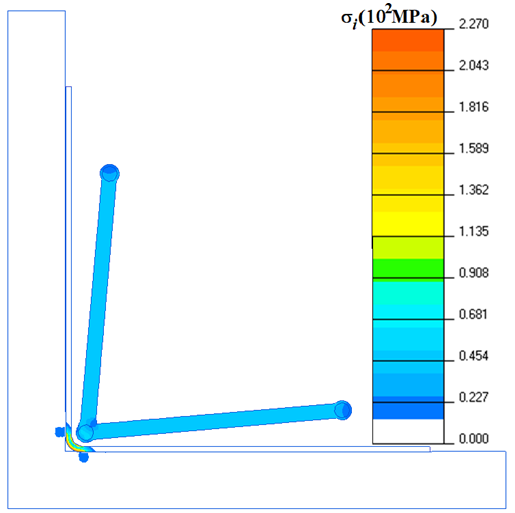
Downloads
Published
How to Cite
Issue
Section
License
Copyright (c) 2024 Yu. I. Zaitsev, D. V. Lavinsky

This work is licensed under a Creative Commons Attribution-NonCommercial 4.0 International License.
Authors who publish with this journal agree to the following terms:
1. Authors retain copyright and grant the journal right of first publication with the work simultaneously licensed under a Creative Commons Attribution License that allows others to share the work with an acknowledgement of the work's authorship and initial publication in this journal.
2. Authors are able to enter into separate, additional contractual arrangements for the non-exclusive distribution of the journal's published version of the work (e.g., post it to an institutional repository or publish it in a book), with an acknowledgement of its initial publication in this journal.
3. Authors are permitted and encouraged to post their work online (e.g., in institutional repositories or on their website) prior to and during the submission process, as it can lead to productive exchanges, as well as earlier and greater citation of published work.