Influence of permanent magnet parameters on the performances of claw pole machines used in hybrid vehicles
DOI:
https://doi.org/10.20998/2074-272X.2024.4.01Keywords:
claw pole machine, permanent magnet dimension, hybrid electric vehicles, finite element method, torque rippleAbstract
Introduction. Claw pole machines (CPM) are commonly used in the automotive industry. Recently, importance has focused on the use and introduction of permanent magnets (PM) in this type of machine to increase the power density. This paper studies the performance of permanent magnet claw pole machines (PM-CPM) used in hybrid electric vehicle applications. The structure considers that the PMs are placed between the claws of the rotor. Purpose. The influence of the PM magnetization effect on the performance of synchronous PM-CPM is analyzed. Radial and tangential magnetizations are applied to obtain the best possible sinusoidal shape of the electromotive force and an acceptable cogging torque. Then, the electromagnetic performance of the PM-CPM is analyzed and evaluated. Furthermore, due to the complexity of the rotor armature, it seems difficult to give a direct relationship between the PM parameters and the machine torque. This led us to study the effects of magnets geometrical dimensions variations on the torque and its ripple. Method. 3D nonlinear model of the machine is analyzed using the finite element method and comparisons between some electromagnetic performances are processed. Results. It was found that the tangential magnetization of PMs makes it possible to obtain a better distribution of the flux density and a minimum of cogging torque mainly responsible for vibrations and acoustic noise. Also, we observed a non-linear variation between the torque and its ripples depending on the dimensions of the PM. In fact, electromagnetic torque increases linearly with PM size but this is not the case for torque ripples. References 22, tables 2, figures 16.
References
Boldea I. Automotive Claw-Pole-Rotor Generator Systems. Variable Speed Generators, Second Edition, CRC Press, 2015, pp. 195-244 doi: https://doi.org/10.1201/b19293-7.
Ibrar A., Ahmad S., Safdar A., Haroon N. Efficiency enhancement strategy implementation in hybrid electric vehicles using sliding mode control. Electrical Engineering & Electromechanics, 2023, no. 1, pp. 10-19. doi: https://doi.org/10.20998/2074-272X.2023.1.02.
Bruyere A., Semail E., Bouscayrol A., Locment F., Dubus J.M., Mipo J.C. Modeling and control of a seven-phase claw-pole integrated starter alternator for micro-hybrid automotive applications. 2008 IEEE Vehicle Power and Propulsion Conference, 2008, pp. 1-6. doi: https://doi.org/10.1109/VPPC.2008.4677668.
Li Y., Yu Z., Meng H., Wang J., Jing Y. Design and Optimization of Hybrid-Excited Claw-Pole Machine for Vehicle. IEEE Transactions on Applied Superconductivity, 2021, vol. 31, no. 8, pp. 1-4. doi: https://doi.org/10.1109/TASC.2021.3094433.
Upadhayay P., Kedous-Lebouc A., Garbuio L., Mipo J.-C., Dubus J.-M. Design & comparison of a conventional and permanent magnet based claw-pole machine for automotive application. 2017 15th International Conference on Electrical Machines, Drives and Power Systems (ELMA), 2017, pp. 1-5. doi: https://doi.org/10.1109/ELMA.2017.7955390.
Bachev I., Lazarov V., Zarkov Z. Analysis of the Influence of NdFeB Permanent Magnet’s Type and Volume on the Characteristics of a PM Claw-pole Alternator. 2021 17th Conference on Electrical Machines, Drives and Power Systems (ELMA), 2021, pp. 1-6. doi: https://doi.org/10.1109/ELMA52514.2021.9502990.
Zhang Z., Liu H., Song T. Optimization Design and Performance Analysis of a PM Brushless Rotor Claw Pole Motor with FEM. Machines, 2016, vol. 4, no. 3, art. no. 15. doi: https://doi.org/10.3390/machines4030015.
Zhao X., Niu S., Ching T.W. Design and Analysis of a New Brushless Electrically Excited Claw-Pole Generator for Hybrid Electric Vehicle. IEEE Transactions on Magnetics, 2018, vol. 54, no. 11, pp. 1-5. doi: https://doi.org/10.1109/TMAG.2018.2823743.
Popa G.N., Maria Dinis C., Baciu I., Deaconu S.I. Automotive PM Surface Alternator, Analyse with Experiments. 2021 International Conference on Applied and Theoretical Electricity (ICATE), 2021, pp. 1-6. doi: https://doi.org/10.1109/ICATE49685.2021.9465009.
Zhao J., Hu C., Zhao Z., Tang M., Tang X. Suitable claw shape design for improving the magnetic properties of forged claw pole parts in generator. IET Electric Power Applications, 2021, vol. 15, no. 10, pp. 1331-1342. doi: https://doi.org/10.1049/elp2.12102.
Wardach M. Hybrid excited claw pole generator with skewed and non-skewed permanent magnets. Open Physics, 2017, vol. 15, no. 1, pp. 902-906. doi: https://doi.org/10.1515/phys-2017-0108.
Tong C., Zheng P., Wu Q., Bai J., Zhao Q. A Brushless Claw-Pole Double-Rotor Machine for Power-Split Hybrid Electric Vehicles. IEEE Transactions on Industrial Electronics, 2014, vol. 61, no. 8, pp. 4295-4305. doi: https://doi.org/10.1109/TIE.2013.2281169.
Geng H., Zhang X., Zhang Y., Hu W., Lei Y., Xu X., Wang A., Wang S., Shi L. Development of Brushless Claw Pole Electrical Excitation and Combined Permanent Magnet Hybrid Excitation Generator for Vehicles. Energies, 2020, vol. 13, no. 18, art. no. 4723. doi: https://doi.org/10.3390/en13184723.
Cao Y., Zhu S., Yu J., Liu C. Optimization Design and Performance Evaluation of a Hybrid Excitation Claw Pole Machine. Processes, 2022, vol. 10, no. 3, art. no. 541. doi: https://doi.org/10.3390/pr10030541.
Fujikura S., Hidaka Y. A Novel Rotor Structure of Claw-pole Motor Designed by Magnetomotive Force-based Simulation Method. IEEJ Journal of Industry Applications, 2020, vol. 9, no. 6, pp. 685-690. doi: https://doi.org/10.1541/ieejjia.20002397.
Bouakacha R., Ouili M., Allag H., Mehasni R., Chebout M., Bouchekara H.R.A. Measurement and three-dimensional calculation of induced electromotive force in permanent magnets heater cylinders. Metrology and Measurement Systems, 2022, vol. 29, no. 2, pp. 315-331. doi: https://doi.org/10.24425/mms.2022.140029.
Phyu H.N., Chao B. Effect of magnetization on high-speed permanent magnet synchronous motor design. 2012 15th International Conference on Electrical Machines and Systems (ICEMS), Sapporo, Japan, 2012, pp. 1-6.
Krishnan R. Permanent Magnet Synchronous and Brushless DC Motor drives. CRC Press, Taylor & Francis Group, 2017. 611 p. doi: https://doi.org/10.1201/9781420014235.
Boutora Y., Takorabet N., Ibtiouen R. Analytical model on real geometries of magnet bars of surface permanent magnet slotless machine. Progress In Electromagnetics Research B, 2016, vol. 66, pp. 31-47. doi: https://doi.org/10.2528/PIERB15121503.
Panchal T.H., Patel A.N., Patel R.M. Reduction of cogging torque of radial flux permanent magnet brushless DC motor by magnet shifting technique. Electrical Engineering & Electromechanics, 2022, no. 3, pp. 15-20. doi: https://doi.org/10.20998/2074-272X.2022.3.03.
Kurihara K., Wakui G., Kubota T. Steady-state performance analysis of permanent magnet synchronous motors including space harmonics. IEEE Transactions on Magnetics, 1994, vol. 30, no. 3, pp. 1306-1315. doi: https://doi.org/10.1109/20.297769.
Cao Y., Zhu S., Yu J., Liu C. Optimization Design and Performance Evaluation of a Hybrid Excitation Claw Pole Machine. Processes, 2022, vol. 10, no. 3, art. no. 541. doi: https://doi.org/10.3390/pr10030541.
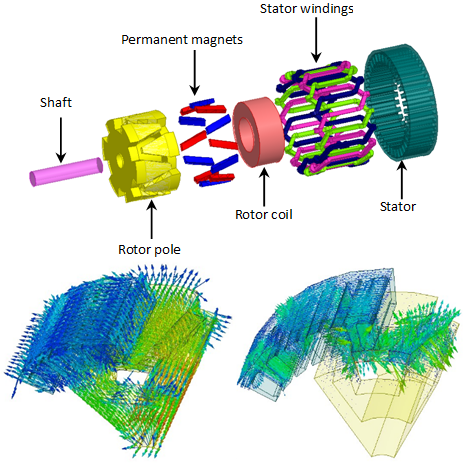
Downloads
Published
How to Cite
Issue
Section
License
Copyright (c) 2024 A. Kimouche, M. R. Mekideche, M. Chebout, H. Allag

This work is licensed under a Creative Commons Attribution-NonCommercial 4.0 International License.
Authors who publish with this journal agree to the following terms:
1. Authors retain copyright and grant the journal right of first publication with the work simultaneously licensed under a Creative Commons Attribution License that allows others to share the work with an acknowledgement of the work's authorship and initial publication in this journal.
2. Authors are able to enter into separate, additional contractual arrangements for the non-exclusive distribution of the journal's published version of the work (e.g., post it to an institutional repository or publish it in a book), with an acknowledgement of its initial publication in this journal.
3. Authors are permitted and encouraged to post their work online (e.g., in institutional repositories or on their website) prior to and during the submission process, as it can lead to productive exchanges, as well as earlier and greater citation of published work.