Numerical-field analysis of active and reactive winding parameters and mechanical characteristics of a squirrel-cage induction motor
DOI:
https://doi.org/10.20998/2074-272X.2023.4.01Keywords:
induction motor, stator and rotor windings, active and reactive resistances, magnetic saturation, eddy currents, mechanical characteristics, classical design, numerical-field calculation analysisAbstract
Introduction. The active and reactive (inductive) winding resistances of three-phase asynchronous motors (IM) are investigated. These important parameters are determined during design and are the basis for calculating a number of energy parameters and characteristics. Problem. In the classical design of IM, the winding resistances are determined with insufficient accuracy due to a number of assumptions and conventions. Especially it concerns the operation of IM with increased slip and it affects the accuracy of realization of its design data, starting parameters and characteristics. Goal. The paper aims to further develop the IM design system by numerical-field computational analysis of active and reactive resistances of the IM windings in the whole range of changes in its slip and calculation of the mechanical characteristic of IM to confirm the adequacy of the calculations of these resistances. Methodology. Resistances of the IM windings are determined by numerous calculations of the magnetic fields of dispersion with the FEMM program within stator and rotor teeth steps, and with current displacement in a squirrel-cage rotor core. Everything is done in the slip range when operating from start-up to idle with changing currents in the slots and the corresponding magnetic saturation of the core teeth. A Lua script has been created for the calculations, controlling the FEMM program and providing automation of all calculations. Results. The numerical-field method shows that the classical design method gives very large errors in determining the magnetic conductivities of IM slot dispersion, as well as current displacement in the bars of the squirrel-cage rotor winding. This is especially evident with increased slips in the start-up mode. Originality. Numerical estimates of the differences between the classical and numerical-field methods are given and the origin of errors is analyzed: the strong saturation of the teeth of the stator and rotor cores. This leads to a significant decrease in the magnetic conductivities of slot dispersion and the practical absence of current displacement in the rotor bars, on which the main emphasis was previously made. The obtained results made it possible to calculate the mechanical characteristic of the IM according to a transparent formula without the use of correction coefficients and reference graphical functions. Practical value. The provided technique of numerical-field analysis and the obtained results of the calculation of active and reactive winding resistances and mechanical characteristic are recommended as a basis for the improvement of the IM design system.
References
Goldberg O.D., Gurin Ya.S., Sviridenko I.S. Design of electrical machines. 2nd ed., revised and additional. Moscow, Higher School Publ., 2001. 430 p. (Rus).
Kopylov I.P., Goryainov F.A., Klokov B.K. Electrical machines designing. Moscow, Yurait Publ., 2011. 767 p. (Rus).
Milykh V.I. Numerically-field analysis of the adequacy of the design data of three-phase induction motors and the method of their refinement on this basis. Technical Electrodynamics, 2018, no. 1, pp. 47-55. (Rus). doi: https://doi.org/10.15407/techned2018.01.047.
Chen H., Bi C. An effective method for determination and characteristic analysis of induction motor parameters. IET Electric Power Applications, 2022, vol. 16, no. 5, pp. 605-615. doi: https://doi.org/10.1049/elp2.12180.
Ermolaev U., Rudenko T. The definition of asynchronous engines parameters with construction of static characteristics for the milling machine tool СФ-АСТРА-РК8 drives. Collection of scientific works of KNTU. Machinery in agricultural production, industrial engineering, automation, 2010, no. 23, pp. 71-77. (Ukr). Available at: http://dspace.kntu.kr.ua/jspui/handle/123456789/1414 (accessed 22 December 2021).
Hachicha M.R., Ben Hadj N., Ghariani M., Neji R. Finite element method for induction machine parameters identification. 2012 First International Conference on Renewable Energies and Vehicular Technology, 2012, pp. 490-496. doi: https://doi.org/10.1109/REVET.2012.6195318.
Muteba M., Jimoh A.A. Performance analysis of a three-phase induction motor with double-triple winding layout. 2013 1st International Future Energy Electronics Conference (IFEEC), 2013, pp. 131-136. doi: https://doi.org/10.1109/IFEEC.2013.6687492.
Yarymbash D.S., Kotsur М.I., Yarymbash S.Т., Kotsur I.М. Features of parameter determination of the induction motor substitution circuit for short-circuit mode. Electrical Engineering and Power Engineering, 2017, no. 1, pp. 24-30. (Rus). doi: https://doi.org/10.15588/1607-6761-2017-1-4.
Tytiuk V., Pozigun O., Chornyi O., Berdai A. Identification of the active resistances of the stator of an induction motor with stator windings dissymmetry. 2017 International Conference on Modern Electrical and Energy Systems (MEES), 2017, pp. 48-51. doi: https://doi.org/10.1109/MEES.2017.8248949.
Tang J., Yang Y., Blaabjerg F., Chen J., Diao L., Liu Z. Parameter Identification of Inverter-Fed Induction Motors: A Review. Energies, 2018, vol. 11, no. 9, art. no. 2194. doi: https://doi.org/10.3390/en11092194.
Bednarz S.A., Dybkowski M. Estimation of the Induction Motor Stator and Rotor Resistance Using Active and Reactive Power Based Model Reference Adaptive System Estimator. Applied Sciences, 2019, vol. 9, no. 23, art. no. 5145. doi: https://doi.org/10.3390/app9235145.
Malyar V.S., Malyar A.V., Andreishyn A.S. A method for calculating mechanical characteristics of induction motors with squirrel-cage rotor. Electrical Engineering & Electromechanics, 2019, no. 2, pp. 9-13. doi: https://doi.org/10.20998/2074-272X.2019.2.02.
Malyar V.S., Hamola O.Y., Maday V.S., Vasylchyshyn I.I. Mathematical modelling of starting modes of induction motors with squirrel-cage rotor. Electrical Engineering & Electromechanics, 2021, no. 2, pp. 9-15. doi: https://doi.org/10.20998/2074-272X.2021.2.02.
Dambrauskas K., Vanagas J., Bugenis S., Zimnickas T., Kalvaitis A. Methodology for Asynchronous Motor Impedance Measurement by Using Higher Order Harmonics. Energies, 2020, vol. 13, no. 10, art. no. 2541. doi: https://doi.org/10.3390/en13102541.
Le Roux P.F., Ngwenyama M.K. Static and Dynamic Simulation of an Induction Motor Using Matlab/Simulink. Energies, 2022, vol. 15, no. 10, art. no. 3564. doi: https://doi.org/10.3390/en15103564.
Finite Element Method Magnetics: OldVersions. FEMM 4.2 11Oct2010 Self-Installing Executable. Available at: http://www.femm.info/wiki/OldVersions (accessed 22 December 2021).
Milykh V.I. The system of automated formation of electrical machines computational models for the FEMM software environment. Technical Electrodynamics. 2018, no. 4, pp. 74-78. (Ukr). doi: https://doi.org/10.15407/techned2018.04.074.
Milykh V.I. Numerical-field analysis of temporal functions and harmonic composition of EMF in windings of a three-phase asynchronous motor. Technical Electrodynamics. 2018, no. 3, pp. 56-65. (Rus). doi: https://doi.org/10.15407/techned2018.03.056.
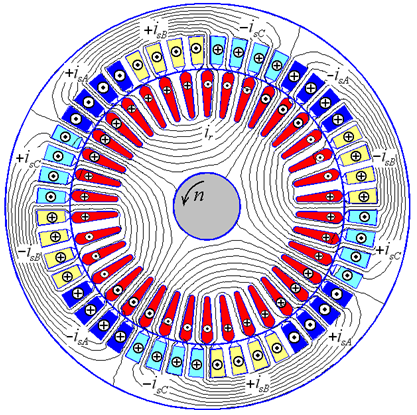
Downloads
Published
How to Cite
Issue
Section
License
Copyright (c) 2023 V. I. Milykh

This work is licensed under a Creative Commons Attribution-NonCommercial 4.0 International License.
Authors who publish with this journal agree to the following terms:
1. Authors retain copyright and grant the journal right of first publication with the work simultaneously licensed under a Creative Commons Attribution License that allows others to share the work with an acknowledgement of the work's authorship and initial publication in this journal.
2. Authors are able to enter into separate, additional contractual arrangements for the non-exclusive distribution of the journal's published version of the work (e.g., post it to an institutional repository or publish it in a book), with an acknowledgement of its initial publication in this journal.
3. Authors are permitted and encouraged to post their work online (e.g., in institutional repositories or on their website) prior to and during the submission process, as it can lead to productive exchanges, as well as earlier and greater citation of published work.