Analysis of the thermal state of the electromagnetic mill inductor with oil cooling in stationary operation modes
DOI:
https://doi.org/10.20998/2074-272X.2023.3.02Keywords:
electromagnetic mill, forced cooling of the inductor with oil, analysis of the thermal state of the mill, method of equivalent thermal circuits, analysis of hydraulic parametersAbstract
Introduction. An electromagnetic mill (EMM) for the technological processing of various substances, which is based on the stator of a three-phase induction motor, is being studied. The stator winding has an increased current density, so the mill is provided with a system of forced cooling with transformer oil. Problem. Currently, there are no works on the thermal state calculation of the EMM with the given design and oil cooling. Therefore, the study of such EMMs thermal state is relevant, as it will contribute to increasing the reliability and efficiency of their work. Goal. Formation of a mathematical model of the thermal state of the electromagnetic mill inductor and the analysis of its heating in stationary modes of operation with cooling by transformer oil. Methodology. The problem of calculating the thermal state, namely the temperature distribution in the main parts of the electromagnetic mill, is solved by the equivalent thermal resistance circuit method. The design of the EMM is provided in a sufficiently complete volume, and on this basis, a corresponding equivalent thermal replacement circuit is formed, which is supplemented by an equivalent hydraulic circuit of oil passageways. An explanation is provided for the composition and solution of the equations algebraic system that describes the distribution of temperatures by the constituent elements of the EMM. Results. The thermal calculation results of the electromagnetic mill showed that the maximum heating temperature is much lower than the allowable one for the selected insulation class. According to the hydraulic scheme, the necessary oil consumption, its average speed and the corresponding pressure at the inlet of the intake pipe are determined, which are at an acceptable level. It is noted that the rather moderate temperature state of the inductor and the hydraulic parameters of the oil path are facilitated by such innovations in the design of the EMM as the loop double layer short chorded winding and axial ventilation channels in the stator core. Originality. Now EMM thermal equivalent circuits with air cooling only have been presented. Therefore, the developed thermal circuit of the oil-cooled inductor is new and makes it possible to evaluate the operating modes of the EMM. Practical value. The proposed technical solutions can be recommended for practical implementation in other EMMs. Taking into account the identified reserves of the EMM temperature state, a forecast was made regarding the transition from its oil cooling to air cooling. But the use of air cooling requires a change in the design of the EMM.
References
Logvinenko D.D., Sheljakov O.P. Intensifikacija tehnologicheskih processov v apparatah s vihrevym sloem [Intensification of technological processes in apparatus with a vortex layer]. Kiev, Tehnika Publ., 1976. 144 p. (Rus).
Voitovich V.A., Kart M.A., Zakharychev E.A., Tarasov S.G. Vortex-layer devices as import-substituting equipment to produce paints and adhesives. Polymer Science, Series D, 2017, vol. 10, no. 2, pp. 153-155. doi: https://doi.org/10.1134/S1995421217020253.
Wolosiewicz-Glab M., Foszcz D., Gawenda T., Ogonowski S. Design of an electromagnetic mill. Its technological and control system structures for dry milling. E3S Web of Conferences, 2016, vol. 8, art. no. 01066. doi: https://doi.org/10.1051/e3sconf/20160801066.
Milykh V.I., Shilkova, L. V. Characteristics of a cylindrical inductor of a rotating magnetic field for technological purposes when it is powered from the mains at a given voltage. Electrical Engineering & Electromechanics, 2020, no. 2, pp. 13-19. doi: https://doi.org/10.20998/2074-272X.2020.2.02.
Ibragimov R.A., Korolev E.V., Kayumov R.A., Deberdeev T.R., Leksin V.V., Sprince A. Efficiency of activation of mineral binders in vortex-layer devices. Magazine of Civil Engineering, 2018, vol. 82, no. 6, pp. 191-198. doi: https://doi.org/10.18720/MCE.82.17.
Wołosiewicz-Głąb M., Foszcz D., Saramak D., Gawenda T., Krawczykowski D. Analysis of a grinding efficiency in the electromagnetic mill for variable process and feed parameters. E3S Web of Conferences, 2017, vol. 18, art. no. 01012. doi: https://doi.org/10.1051/e3sconf/20171801012.
Całus D., Makarchuk O. Analysis of interaction of forces of working elements in electromagnetic mill. Przegląd Elektrotechniczny, 2019, vol. 95, no. 12, pp. 64-69. doi: https://doi.org/10.15199/48.2019.12.12.
Wołosiewicz-Głąb M., Pięta P., Foszcz D., Niedoba T., Gawenda T. Adjustment of limestone grinding in an electromagnetic mill for use in production of sorbents for flue gas desulphurization. Physicochemical Problems of Mineral Processing, 2019, vol. 55, no. 3, pp. 779-791. doi: https://doi.org/10.5277/ppmp19011.
Ogonowski S., Wołosiewicz-Głąb M., Ogonowski Z., Foszcz D., Pawełczyk M. Comparison of Wet and Dry Grinding in Electromagnetic Mill. Minerals, 2018, vol. 8, no. 4, art. no. 138. doi: https://doi.org/10.3390/min8040138.
Zhakirova N., Salakhov R., Sassykova L., Khamidullin R., Deberdeev T., Yalyshev U., Khamidi A., Seilkhanov T. Increasing the Yield of Light Distillates by Wave Action on Oil Raw Materials. Eurasian Chemico-Technological Journal, 2021, vol. 23, no. 2, pp. 125-132. doi: https://doi.org/10.18321/ectj1083.
Kovalev A.A., Kovalev D.A., Grigoriev V.S., Litti Y.V. The vortex layer apparatus as a source of low-grade heat in the process of pretreatment of the substrate before anaerobic digestion. IOP Conference Series: Earth and Environmental Science, 2021, vol. 938, no. 1, art. no. 012004. doi: https://doi.org/10.1088/1755-1315/938/1/012004.
Mixing machine AVS-100. Electromagnetic mill. Available at: https://globecore.com/products/magnetic-mill/mixing-machine-avs-100/ (Accessed 20.02.2022).
Ogonowski S., Ogonowski Z., Pawełczyk M. Multi-Objective and Multi-Rate Control of the Grinding and Classification Circuit with Electromagnetic Mill. Applied Sciences, 2018, vol. 8, no. 4, art. no. 506. doi: https://doi.org/10.3390/app8040506.
Krawczykowski D., Foszcz D., Ogonowski S., Gawenda T., Wołosiewicz-Głąb M. Analysis of the working chamber size influence on the effectiveness of grinding in electromagnetic mill. IOP Conference Series: Materials Science and Engineering, 2018, vol. 427, art. no. 012033. doi: https://doi.org/10.1088/1757-899X/427/1/012033.
Ogonowski S. On-Line Optimization of Energy Consumption in Electromagnetic Mill Installation. Energies, 2021, vol. 14, no. 9, art. no. 2380. doi: https://doi.org/10.3390/en14092380.
Styła S., Mańko M. A reluctance model of an electromagnetic mill using the stator of an asynchronous motor as an inductor. Przegląd Elektrotechniczny, 2020, vol. 96, no. 1, pp. 254-257. doi: https://doi.org/10.15199/48.2020.01.58.
Milykh V.I., Shilkova L.V. Numerical-experimental analysis of the magnetic field of a magnetic separator inductor on the basis of an asynchronous motor. Bulletin of NTU «KhPI». Series: Electric machines and electromechanical energy conversion, 2018, no. 5 (1281), pp. 104-109. (Ukr).
Makarchuk O., Calus D., Moroz V. Mathematical model to calculate the trajectories of electromagnetic mill operating elements. Technical Electrodynamics, 2021, no. 2, pp. 26-34. doi: https://doi.org/10.15407/techned2021.02.026.
Milykh V.I., Shilkova L.V. Control current method of the concentration of ferromagnetic elements in the working chamber of the technological inductor of magnetic field during its operation. Electrical Engineering & Electromechanics, 2020, no. 5, pp. 12-17. doi: https://doi.org/10.20998/2074-272X.2020.5.02.
Shcherban’ E.M., Stel’makh S.A., Beskopylny A., Mailyan L.R., Meskhi B., Shuyskiy A. Improvement of Strength and Strain Characteristics of Lightweight Fiber Concrete by Electromagnetic Activation in a Vortex Layer Apparatus. Applied Sciences, 2021, vol. 12, no. 1, art. no. 104. doi: https://doi.org/10.3390/app12010104.
Krauze O., Buchczik D., Budzan S. Measurement-Based Modelling of Material Moisture and Particle Classification for Control of Copper Ore Dry Grinding Process. Sensors, 2021, vol. 21, no. 2, art. no. 667. doi: https://doi.org/10.3390/s21020667.
Styła S. Analysis of temperature distribution in electromagnetic mill. Przegląd Elektrotechniczny, 2016, vol. 92, no. 3, pp. 103-106. doi: https://doi.org/10.15199/48.2016.03.25.
Vlasov A.B., Mukhin E.A. Methodology for calculating the temperature of the windings of an electric machine based on quantitative thermography. Vestnik of MSTU, 2011, vol. 14, no. 4, pp. 671-680. (Rus).
Yang Y., Bilgin B., Kasprzak M., Nalakath S., Sadek H., Preindl M., Cotton J., Schofield N., Emadi A. Thermal management of electric machines. IET Electrical Systems in Transportation, 2017, vol. 7, no. 2, pp. 104-116. doi: https://doi.org/10.1049/iet-est.2015.0050.
Lundmark S.T., Acquaviva A., Bergqvist A. Coupled 3-D Thermal and Electromagnetic Modelling of a Liquid-cooled Transverse Flux Traction Motor. 2018 XIII International Conference on Electrical Machines (ICEM), 2018, pp. 2640-2646. doi: https://doi.org/10.1109/ICELMACH.2018.8506835.
Milykh V.I., Tymin M.G. A comparative analysis of the parameters of a rotating magnetic field inductor when using concentric and loop windings. Electrical Engineering & Electromechanics, 2021, no. 4, pp. 12-18. doi: https://doi.org/10.20998/2074-272X.2021.4.02.
Ostashevskiy N.A., Shayda V.P., Petrenko A.N. Research into thermal state of a frequency-controlled asynchronous motor by means of a finite element method. Electrical Engineering & Electromechanics, 2011, no. 5, pp. 39-42. (Rus).
Kazi S.N. (Ed.) Heat Transfer Phenomena and Applications. London, United Kingdom, IntechOpen, 2012. doi: https://doi.org/10.5772/3391.
Ostashevskiy N.A., Petrenko A.N., Yurieva O.Yu. Teplovi rozrakhunky elektrychnykh mashyn [Thermal calculations of electric machines]. Kharkiv, O.M. Beketov NUUEKh Publ., 2020. 450 p. (Ukr).
The Engineering ToolBox. Available at: https://www.engineeringtoolbox.com (Accessed 20.02.2022).
Materials Thermal Properties Database. Available at: https://thermtest.com/thermal-resources/materials-database (Accessed 20.02.2022).
Duong M.T., Chun Y.-D., Park B.-G, Kim D.-J, Choi J.-H, Han P.-W. Thermal analysis of a high speed induction motor considering harmonic loss distribution. Journal of Electrical Engineering and Technology, 2017, vol. 12. pp. 1503-1510. doi: https://doi.org/10.5370/JEET.2017.12.4.1503.
Shams Ghahfarokhi P., Podgornovs A., Kallaste A., Cardoso A.J.M., Belahcen A., Vaimann T., Asad B., Tiismus H. Determination of Heat Transfer Coefficient from Housing Surface of a Totally Enclosed Fan-Cooled Machine during Passive Cooling. Machines, 2021, vol. 9, no. 6, art. no. 120. doi: https://doi.org/10.3390/machines9060120.
SMath Studio. Available at: https://smath.com (Accessed 20.02.2022).
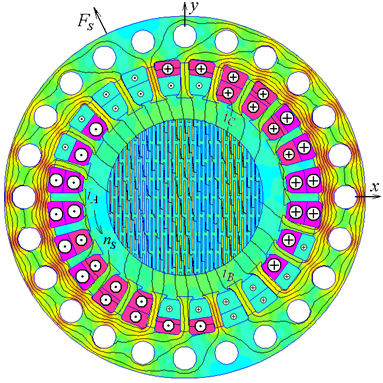
Downloads
Published
How to Cite
Issue
Section
License
Copyright (c) 2023 V. I. Milykh, V. Р. Shaida, O. Yu. Yurieva

This work is licensed under a Creative Commons Attribution-NonCommercial 4.0 International License.
Authors who publish with this journal agree to the following terms:
1. Authors retain copyright and grant the journal right of first publication with the work simultaneously licensed under a Creative Commons Attribution License that allows others to share the work with an acknowledgement of the work's authorship and initial publication in this journal.
2. Authors are able to enter into separate, additional contractual arrangements for the non-exclusive distribution of the journal's published version of the work (e.g., post it to an institutional repository or publish it in a book), with an acknowledgement of its initial publication in this journal.
3. Authors are permitted and encouraged to post their work online (e.g., in institutional repositories or on their website) prior to and during the submission process, as it can lead to productive exchanges, as well as earlier and greater citation of published work.