Optimization of cogging torque in interior permanent magnet synchronous motor using optimum magnet v-angle
DOI:
https://doi.org/10.20998/2074-272X.2023.6.03Keywords:
cogging torque, finite element analysis, interior v-shape web, magnet spread angle, magnet v-angle, permanent magnet synchronous motorAbstract
Introduction. At present, the most important requirement in the field of electrical engineering is the better utilization of electrical power, due to its increasing demand and not-so-increasing availability. A permanent magnet synchronous motor (PMSM) is increasingly gaining popularity in various household and industrial applications because of its superior performance compared to conventional electrical motors. Purpose. PMSM is designed based on the selection of various design variables and optimized to fulfill the same. Being superiorly advantageous over other motors, PMSM has the major disadvantage of higher cogging torque. Higher cogging torque generates torque ripple in the PMSM motor leading to various problems like vibration, rotor stress, and noisy operation during starting and steady state. The designer should aim to reduce the cogging torque at the design stage itself for overall better performance. Methods. An interior rotor v-shaped web-type PMSM is designed and its performance analysis is carried out using finite element analysis (FEA). Magnet v-angle is optimized with the objective of cogging torque reduction. Performance comparison is carried out between the optimized motor and the initially designed motor with FEA. Novelty. Magnet v-angle analysis is performed on the same keeping all other parameters constant, to obtain minimum cogging torque. The proposed method is practically viable as it does not incur extra costs and manufacturing complexity. Practical value. It is observed that the magnet v-angle is an effective technique in the reduction of cogging torque. Cogging torque is reduced from 0.554 N×m to 0.452 N×m with the application of the magnet v-angle optimization technique.
References
Pillay P., Krishnan R. Application characteristics of permanent magnet synchronous and brushless DC motors for servo drives. IEEE Transactions on Industry Applications, 1991, vol. 27, no. 5, pp. 986-996. doi: https://doi.org/10.1109/28.90357.
Panchal T.H., Patel A.N., Patel R.M. Reduction of cogging torque of radial flux permanent magnet brushless DC motor by magnet shifting technique. Electrical Engineering & Electromechanics, 2022, no. 3, pp. 15-20. doi: https://doi.org/10.20998/2074-272X.2022.3.03.
Ge X., Zhu Z.Q., Kemp G., Moule D., Williams C. Optimal Step-Skew Methods for Cogging Torque Reduction Accounting for Three-Dimensional Effect of Interior Permanent Magnet Machines. IEEE Transactions on Energy Conversion, 2017, vol. 32, no. 1, pp. 222-232. doi: https://doi.org/10.1109/TEC.2016.2620476.
Touzhu Li, Slemon G. Reduction of cogging torque in permanent magnet motors. IEEE Transactions on Magnetics, 1988, vol. 24, no. 6, pp. 2901-2903. doi: https://doi.org/10.1109/20.92282.
Ishikawa T., Slemon G.R. A method of reducing ripple torque in permanent magnet motors without skewing. IEEE Transactions on Magnetics, 1993, vol. 29, no. 2, pp. 2028-2031. doi: https://doi.org/10.1109/20.250808.
Zhu Z.Q., Howe D. Influence of design parameters on cogging torque in permanent magnet machines. IEEE Transactions on Energy Conversion, 2000, vol. 15, no. 4, pp. 407-412. doi: https://doi.org/10.1109/60.900501.
Zhu Q., Ruangsinchaiwanich S., Schofield N., Howe D. Reduction of cogging torque in interior-magnet brushless machines. IEEE Transactions on Magnetics, 2003, vol. 39, no. 5, pp. 3238-3240. doi: https://doi.org/10.1109/TMAG.2003.816733.
Lai C., Feng G., Iyer K.L.V., Mukherjee K., Kar N.C. Genetic Algorithm-Based Current Optimization for Torque Ripple Reduction of Interior PMSMs. IEEE Transactions on Industry Applications, 2017, vol. 53, no. 5, pp. 4493-4503. doi: https://doi.org/10.1109/TIA.2017.2704063.
Luu P.T., Lee J.-Y., Hwang W., Woo B.-C. Cogging Torque Reduction Technique by Considering Step-Skew Rotor in Permanent Magnet Synchronous Motor. 2018 21st International Conference on Electrical Machines and Systems (ICEMS), 2018, pp. 219-223. doi: https://doi.org/10.23919/ICEMS.2018.8549086.
Park G.-J., Kim Y.-J., Jung S.-Y. Design of IPMSM Applying V-Shape Skew Considering Axial Force Distribution and Performance Characteristics According to the Rotating Direction. IEEE Transactions on Applied Superconductivity, 2016, vol. 26, no. 4, pp. 1-5. doi: https://doi.org/10.1109/TASC.2016.2543267.
Jiang J.W., Bilgin B., Yang Y., Sathyan A., Dadkhah H., Emadi A. Rotor skew pattern design and optimisation for cogging torque reduction. IET Electrical Systems in Transportation, 2016, vol. 6, no. 2, pp. 126-135. doi: https://doi.org/10.1049/iet-est.2015.0021.
Nur T., Mulyadi M. Improve cogging torque method in inset-permanent magnet synchronous machine. 2018 IEEE International Conference on Applied System Invention (ICASI), 2018, pp. 1211-1213. doi: https://doi.org/10.1109/ICASI.2018.8394506.
Jae Yoon Oh, Dal Ho Jung. Flux Barrier Synchronous Reluctance Motor. USA Patent no. 6239526B1, May 29, 2001.
Kawaguchi Y., Sato T., Miki I., Nakamura M. A reduction method of cogging torque for IPMSM. 2005 International Conference on Electrical Machines and Systems, 2005, vol. 1, pp. 248-250. doi: https://doi.org/10.1109/ICEMS.2005.202522.
Kano Y. Sensorless-oriented design of IPMSM. 2014 International Power Electronics Conference (IPEC-Hiroshima 2014 - ECCE ASIA), 2014, pp. 2457-2464. doi: https://doi.org/10.1109/IPEC.2014.6869934.
Rahimi Monjezi S., Kiyoumarsi A., Mirzaeian Dehkordi B., Sabahi M.-F., Vafaie M.-H. Shape Design Optimization of Interior Permanent-Magnet Synchronous Motor with Machaon Flux Barriers for Reduction of Torque Pulsation. Electric Power Components and Systems, 2016, vol. 44, no. 19, pp. 2212-2223. doi: https://doi.org/10.1080/15325008.2016.1199611.
Du Z.S., Lipo T.A. Reducing Torque Ripple Using Axial Pole Shaping in Interior Permanent Magnet Machines. IEEE Transactions on Industry Applications, 2020, vol. 56, no. 1, pp. 148-157. doi: https://doi.org/10.1109/TIA.2019.2946237.
Ugale R.T., Chaudhari B.N., Baka S., Pramanik A. A Hybrid Interior Rotor High-performance Line Start Permanent Magnet Synchronous Motor. Electric Power Components and Systems, 2014, vol. 42, no. 9, pp. 901-913. doi: https://doi.org/10.1080/15325008.2014.903539.
Hanselman D.C. Brushless Permanent Magnet Motor Design. Magna Physics Publ., Ohio, 2006. 411 p.
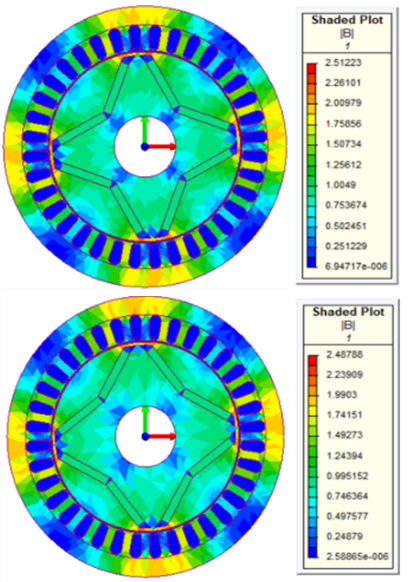
Downloads
Published
How to Cite
Issue
Section
License
Copyright (c) 2023 A. N. Patel, P. J. Doshi, S. C. Mahagaokar, T. H. Panchal

This work is licensed under a Creative Commons Attribution-NonCommercial 4.0 International License.
Authors who publish with this journal agree to the following terms:
1. Authors retain copyright and grant the journal right of first publication with the work simultaneously licensed under a Creative Commons Attribution License that allows others to share the work with an acknowledgement of the work's authorship and initial publication in this journal.
2. Authors are able to enter into separate, additional contractual arrangements for the non-exclusive distribution of the journal's published version of the work (e.g., post it to an institutional repository or publish it in a book), with an acknowledgement of its initial publication in this journal.
3. Authors are permitted and encouraged to post their work online (e.g., in institutional repositories or on their website) prior to and during the submission process, as it can lead to productive exchanges, as well as earlier and greater citation of published work.