Slot opening displacement technique for cogging torque reduction of axial flux brushless DC motor for electric two-wheeler application
DOI:
https://doi.org/10.20998/2074-272X.2023.2.02Keywords:
axial flux brushless DC motor, cogging torque, slot opening displacement, design improvement, finite element analysisAbstract
Introduction. Reduction of cogging torque is the crucial design consideration of axial flux brushless DC (BLDC) motor, particularly for low-speed applications. Aim. The slot opening displacement technique is presented in this article to reduce cogging torque in axial flux BLDC motors suitable for electric two-wheeler applications. Methods. Double rotor single stator configuration of axial flux BLDC motor is the most suitable for such vehicular applications. Initially double rotor single stator 250 W, 150 rpm axial flux BLDC motor is designed with stator slot opening in middle position and considered as reference motor for further analysis. To evaluate the cogging torque profile of the reference motor 3D finite element modeling and analysis are performed. The design is enhanced by dividing all stator teeth into groups and displacing the slot openings of each group in opposite direction with respect to the adjacent group. Results. The influence of slot opening displacement on cogging torque is evaluated with finite element modeling and analysis. As cogging torque is reduced from 1.23 N×m to 0.63 N×m, the slot opening displacement technique is found to be effective in reducing cogging torque of axial flux BLDC motor.
References
Akkouchi K., Rahmani L., Lebied R. New application of artificial neural network-based direct power control for permanent magnet synchronous generator. Electrical Engineering & Electromechanics, 2021, no. 6, pp. 18-24. doi: https://doi.org/10.20998/2074-272X.2021.6.03.
Panchal T.H., Patel A.N., Patel R.M. Reduction of cogging torque of radial flux permanent magnet brushless DC motor by magnet shifting technique. Electrical Engineering & Electromechanics, 2022, no. 3, pp. 15-20. doi: https://doi.org/10.20998/2074-272X.2022.3.03
Chan C.C. Axial-Field Electrical Machines - Design and Applications. IEEE Transactions on Energy Conversion, 1987, vol. EC-2, no. 2, pp. 294-300. doi: https://doi.org/10.1109/TEC.1987.4765844.
Aydin M., Huang S., Lipo T. A. Axial Flux Permanent Magnet Disc Machines: A Review. Research Report, 2004, no. 10, pp. 1-11.
Rahim N.A., Ping H.W., Tadjuddin M. Design of Axial Flux Permanent Magnet Brushless DC Motor for Direct Drive of Electric Vehicle. 2007 IEEE Power Engineering Society General Meeting, 2007, pp. 1-6. doi: https://doi.org/10.1109/PES.2007.385615.
Aydin M., Zhu Z.Q., Lipo T.A., Howe D. Minimization of Cogging Torque in Axial-Flux Permanent-Magnet Machines: Design Concepts. IEEE Transactions on Magnetics, 2007, vol. 43, no. 9, pp. 3614-3622. doi: https://doi.org/10.1109/TMAG.2007.902818.
Islam R., Husain I., Fardoun A., McLaughlin K. Permanent Magnet Synchronous Motor Magnet Designs with Skewing for Torque Ripple and Cogging Torque Reduction. 2007 IEEE Industry Applications Annual Meeting, 2007, pp. 1552-1559. doi: https://doi.org/10.1109/07IAS.2007.240.
Chu W.Q., Zhu Z.Q. Investigation of Torque Ripples in Permanent Magnet Synchronous Machines With Skewing. IEEE Transactions on Magnetics, 2013, vol. 49, no. 3, pp. 1211-1220. doi: https://doi.org/10.1109/TMAG.2012.2225069.
Chabchoub M., Ben Salah I., Krebs G., Neji R., Marchand C. PMSM cogging torque reduction: Comparison between different shapes of magnet. 2012 First International Conference on Renewable Energies and Vehicular Technology, 2012, pp. 206-211. doi: https://doi.org/10.1109/REVET.2012.6195272.
Jong Gun Lee, Yu Ki Lee, Gwan Soo Park. Effects of V-skew on the cogging torque in permanent magnet synchronous motor. 2013 International Conference on Electrical Machines and Systems (ICEMS), 2013, pp. 122-124. doi: https://doi.org/10.1109/ICEMS.2013.6754536.
Boukais B., Zeroug H. Magnet Segmentation for Commutation Torque Ripple Reduction in a Brushless DC Motor Drive. IEEE Transactions on Magnetics, 2010, vol. 46, no. 11, pp. 3909-3919. doi: https://doi.org/10.1109/TMAG.2010.2057439.
Wenliang Zhao, Lipo T.A., Byung-Il Kwon. Material-Efficient Permanent-Magnet Shape for Torque Pulsation Minimization in SPM Motors for Automotive Applications. IEEE Transactions on Industrial Electronics, 2014, vol. 61, no. 10, pp. 5779-5787. doi: https://doi.org/10.1109/TIE.2014.2301758.
Bin Zhang, Xiuhe Wang, Ran Zhang, Xiaolei Mou. Cogging torque reduction by combining teeth notching and rotor magnets skewing in PM BLDC with concentrated windings. 2008 International Conference on Electrical Machines and Systems, 2008, pp. 3189-3192.
Petrov I., Ponomarev P., Alexandrova Y., Pyrhonen J. Unequal Teeth Widths for Torque Ripple Reduction in Permanent Magnet Synchronous Machines With Fractional-Slot Non-Overlapping Windings. IEEE Transactions on Magnetics, 2015, vol. 51, no. 2, pp. 1-9. doi: https://doi.org/10.1109/TMAG.2014.2355178.
Park G.-J., Kim Y.-J., Jung S.-Y. Design of IPMSM Applying V-Shape Skew Considering Axial Force Distribution and Performance Characteristics According to the Rotating Direction. IEEE Transactions on Applied Superconductivity, 2016, vol. 26, no. 4, pp. 1-5. doi: https://doi.org/10.1109/TASC.2016.2543267.
Upadhayay P., Rajagopal K.R. Torque ripple reduction using magnet pole shaping in a surface mounted Permanent Magnet BLDC motor. 2013 International Conference on Renewable Energy Research and Applications (ICRERA), 2013, pp. 516-521. doi: https://doi.org/10.1109/ICRERA.2013.6749809.
Sarac V. Performance optimization of permanent magnet synchronous motor by cogging torque reduction. Journal of Electrical Engineering, 2019, vol. 70, no. 3, pp. 218-226. doi: https://doi.org/10.2478/jee-2019-0030.
Yu H.-C., Yu B.-S., Yu J., Lin C.-K. A Dual Notched Design of Radial-Flux Permanent Magnet Motors with Low Cogging Torque and Rare Earth Material. IEEE Transactions on Magnetics, 2014, vol. 50, no. 11, pp. 1-4. doi: https://doi.org/10.1109/TMAG.2014.2329139.
Aydin M., Gulec M. Reduction of Cogging Torque in Double-Rotor Axial-Flux Permanent-Magnet Disk Motors: A Review of Cost-Effective Magnet-Skewing Techniques With Experimental Verification. IEEE Transactions on Industrial Electronics, 2014, vol. 61, no. 9, pp. 5025-5034. doi: https://doi.org/10.1109/TIE.2013.2276777.
Park G.-J., Kim Y.-J., Jung S.-Y. Design of IPMSM Applying V-Shape Skew Considering Axial Force Distribution and Performance Characteristics According to the Rotating Direction. IEEE Transactions on Applied Superconductivity, 2016, vol. 26, no. 4, pp. 1-5. doi: https://doi.org/10.1109/TASC.2016.2543267.
Jia L., Lin M., Le W., Li N., Kong Y. Dual-Skew Magnet for Cogging Torque Minimization of Axial Flux PMSM With Segmented Stator. IEEE Transactions on Magnetics, 2020, vol. 56, no. 2, pp. 1-6. doi: https://doi.org/10.1109/TMAG.2019.2951704.
Wanjiku J., Khan M.A., Barendse P.S., Pillay P. Influence of Slot Openings and Tooth Profile on Cogging Torque in Axial-Flux PM Machines. IEEE Transactions on Industrial Electronics, 2015, vol. 62, no. 12, pp. 7578-7589. doi: https://doi.org/10.1109/TIE.2015.2458959.
Kumar P., Srivastava R.K. Cost-Effective Stator Modification Techniques for Cogging Torque Reduction in Axial Flux Permanent Magnet Machines. 2018 IEEE Transportation Electrification Conference and Expo, Asia-Pacific (ITEC Asia-Pacific), 2018, pp. 1-5. doi: https://doi.org/10.1109/ITEC-AP.2018.8433291.
Patel A.N., Suthar B.N. Cogging Torque Reduction of Sandwiched Stator Axial Flux Permanent Magnet Brushless DC Motor using Magnet Notching Technique. International Journal of Engineering, 2019, vol. 32, no. 7, pp. 940-946. doi: https://doi.org/10.5829/ije.2019.32.07a.06.
Dosiek L., Pillay P. Cogging Torque Reduction in Permanent Magnet Machines. IEEE Transactions on Industry Applications, 2007, vol. 43, no. 6, pp. 1565-1571. doi: https://doi.org/10.1109/TIA.2007.908160.
Surong Huang, Jian Luo, Leonardi F., Lipo T.A. A general approach to sizing and power density equations for comparison of electrical machines. IEEE Transactions on Industry Applications, 1998, vol. 34, no. 1, pp. 92-97. doi: https://doi.org/10.1109/28.658727.
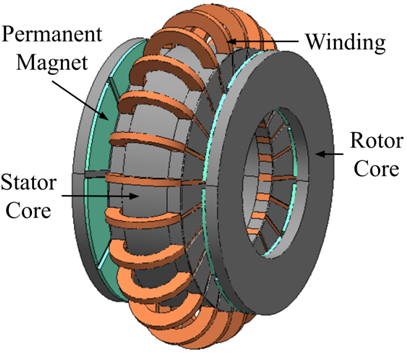
Downloads
Published
How to Cite
Issue
Section
License
Copyright (c) 2022 A. N. Patel

This work is licensed under a Creative Commons Attribution-NonCommercial 4.0 International License.
Authors who publish with this journal agree to the following terms:
1. Authors retain copyright and grant the journal right of first publication with the work simultaneously licensed under a Creative Commons Attribution License that allows others to share the work with an acknowledgement of the work's authorship and initial publication in this journal.
2. Authors are able to enter into separate, additional contractual arrangements for the non-exclusive distribution of the journal's published version of the work (e.g., post it to an institutional repository or publish it in a book), with an acknowledgement of its initial publication in this journal.
3. Authors are permitted and encouraged to post their work online (e.g., in institutional repositories or on their website) prior to and during the submission process, as it can lead to productive exchanges, as well as earlier and greater citation of published work.