Reduction of cogging torque of radial flux permanent magnet brushless DC motor by magnet shifting technique
DOI:
https://doi.org/10.20998/2074-272X.2022.3.03Keywords:
cogging torque, finite element analysis, magnet shifting, permanent magnet brushless DC motorAbstract
Introduction. In spite of many advantages of radial flux permanent magnet brushless DC motors it suffers from the distinct disadvantage of high cogging torque. The designer must emphasize to reduce the cogging torque during the design stage. This paper introduces magnet shifting technique to mitigate cogging torque of surface mounted radial flux brushless DC motor. Methodology. Initially 200 W, 1000 rpm surface mounted radial flux permanent magnet brushless DC motor is designed with symmetrical placement of permanent magnets with respect to each other on rotor core. Cogging torque profile of this initial motor is obtained by performing finite element modelling and analysis. Originality. This design has been improved by shifting the position of permanent magnets with respect to adjacent permanent magnets. The effect of magnet shifting on cogging torque has been analyzed by performing finite element analysis. Results. It has been examined that the peak to peak cogging torque is decreased from 1.1 N×m to 0.6 N×m with shifting of permanent magnets respectively.
References
D. C. Hanselman, Brushless Permanent Magnet Motor Design, New York, McGraw- Hill, 1994.
Akkouchi K., Rahmani L., Lebied R. New application of artificial neural network-based direct power control for permanent magnet synchronous generator. Electrical Engineering & Electromechanics, 2021, no. 6, pp. 18-24. doi: https://doi.org/10.20998/2074-272X.2021.6.03.
Liu Ronghui, Wang Rumei, Li Jiebao. Reduction of cogging torque in surfacemounted permanent magnet brushless motor based on Motorsolve. IEEE PES Innovative Smart Grid Technologies, 2012, pp. 1–4. doi: https://doi.org/10.1109/ISGT-Asia.2012.6303245.
Liu T., Huang S., Gao J., Lu K. Cogging Torque Reduction by Slot-Opening Shift for Permanent Magnet Machines. IEEE Transactions on Magnetics, 2013, vol. 49, no. 7, pp. 4028-4031. doi: https://doi.org/10.1109/TMAG.2013.2239977.
Seo J.-D., Yoo J.-H., Jung T.-U. Design on notch structure of stator tooth to reduce of cogging torque of single-phase BLDC motor. 2015 18th International Conference on Electrical Machines and Systems (ICEMS), 2015, pp. 1475-1478. doi: https://doi.org/10.1109/ICEMS.2015.7385273.
Chabchoub M., Ben Salah I., Krebs G., Neji R., Marchand C. PMSM cogging torque reduction: Comparison between different shapes of magnet. 2012 First International Conference on Renewable Energies and Vehicular Technology, 2012, pp. 206-211. doi: https://doi.org/10.1109/REVET.2012.6195272.
Islam M.S., Mir S., Sebastian T. Issues in reducing the cogging torque of mass-produced permanent magnet brushless DC motor. 38th IAS Annual Meeting on Conference Record of the Industry Applications Conference, 2003, vol. 1, pp. 393-400. doi: https://doi.org/10.1109/IAS.2003.1257531.
Yu H.-C., Yu B.-S., Yu J., Lin C.-K. A Dual Notched Design of Radial-Flux Permanent Magnet Motors with Low Cogging Torque and Rare Earth Material. IEEE Transactions on Magnetics, 2014, vol. 50, no. 11, pp. 1-4. doi: https://doi.org/10.1109/TMAG.2014.2329139.
Srisiriwanna T., Konghirun M. A study of cogging torque reduction methods in brushless dc motor. 2012 9th International Conference on Electrical Engineering/Electronics, Computer, Telecommunications and Information Technology, 2012, pp. 1-4. doi: https://doi.org/10.1109/ECTICon.2012.6254191.
Zhang B., Wang X., Zhang R., Mou X. Cogging torque reduction by combining teeth notching and rotor magnets skewing in PM BLDC with concentrated windings. 2008 International Conference on Electrical Machines and Systems, 2008, pp. 3189-3192.
Setiabudy R., Wahab H., Putra Y.S. Reduction of cogging torque on brushless direct current motor with segmentation of magnet permanent. 2017 4th International Conference on Information Technology, Computer, and Electrical Engineering (ICITACEE), 2017, pp. 81-86. doi: https://doi.org/10.1109/ICITACEE.2017.8257680.
Karnavas Y.L., Chasiotis I.D., Gkiokas A.D. An Investigation Study Considering the Effect of Magnet Type, Slot Type and Pole-Arc to Pole-Pitch Ratio Variation on PM Brushless DC Motor Design. 2018 5th International Conference on Mathematics and Computers in Sciences and Industry (MCSI), 2018, pp. 7-13. doi: https://doi.org/10.1109/MCSI.2018.00010.
Ki-Jin Han, Han-Sam Cho, Dong-Hyeok Cho, Hyun-Kyo Jung. Optimal core shape design for cogging torque reduction of brushless DC motor using genetic algorithm. IEEE Transactions on Magnetics, 2000, vol. 36, no. 4, pp. 1927-1931. doi: https://doi.org/10.1109/20.877824.
Wang A., Ma D., Shu S. Influence of magnet pole shifting on cogging torque for PMSG application. 2014 17th International Conference on Electrical Machines and Systems (ICEMS), 2014, pp. 495-499. doi: https://doi.org/10.1109/ICEMS.2014.7013521.
Islam R., Husain I., Fardoun A., McLaughlin K. Permanent Magnet Synchronous Motor Magnet Designs with Skewing for Torque Ripple and Cogging Torque Reduction. 2007 IEEE Industry Applications Annual Meeting, 2007, pp. 1552-1559. doi: https://doi.org/10.1109/07IAS.2007.240.
Boukais B., Zeroug H. Magnet Segmentation for Commutation Torque Ripple Reduction in a Brushless DC Motor Drive. IEEE Transactions on Magnetics, 2010, vol. 46, no. 11, pp. 3909-3919. doi: https://doi.org/10.1109/TMAG.2010.2057439.
Nur T., Haroen Y. Investigation the influence of magnet slots with fixed slot opening width on the cogging torque of Inset-PMSM. The 2nd IEEE Conference on Power Engineering and Renewable Energy (ICPERE) 2014, pp. 195-197. doi: https://doi.org/10.1109/ICPERE.2014.7067211.
Petrov I., Ponomarev P., Alexandrova Y., Pyrhonen J. Unequal Teeth Widths for Torque Ripple Reduction in Permanent Magnet Synchronous Machines With Fractional-Slot Non-Overlapping Windings. IEEE Transactions on Magnetics, 2015, vol. 51, no. 2, pp. 1-9. doi: https://doi.org/10.1109/TMAG.2014.2355178.
Dosiek L., Pillay P. (). Cogging Torque Reduction in Permanent Magnet Machines. IEEE Transactions on Industry Applications, 2007, vol. 43, no. 6, pp. 1565-1571. doi: https://doi.org/10.1109/TIA.2007.908160.
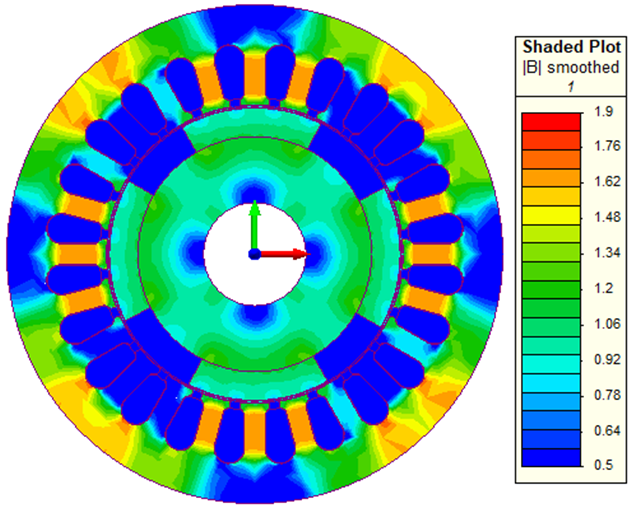
Downloads
Published
How to Cite
Issue
Section
License
Copyright (c) 2022 T. H. Panchal, A. N. Patel, R. M. Patel

This work is licensed under a Creative Commons Attribution-NonCommercial 4.0 International License.
Authors who publish with this journal agree to the following terms:
1. Authors retain copyright and grant the journal right of first publication with the work simultaneously licensed under a Creative Commons Attribution License that allows others to share the work with an acknowledgement of the work's authorship and initial publication in this journal.
2. Authors are able to enter into separate, additional contractual arrangements for the non-exclusive distribution of the journal's published version of the work (e.g., post it to an institutional repository or publish it in a book), with an acknowledgement of its initial publication in this journal.
3. Authors are permitted and encouraged to post their work online (e.g., in institutional repositories or on their website) prior to and during the submission process, as it can lead to productive exchanges, as well as earlier and greater citation of published work.