Mutual influence of currents in plane inductor system with solenoid between two massive conductors
DOI:
https://doi.org/10.20998/2074-272X.2021.6.04Keywords:
magnetic-pulse stamping, sheet metals, electromagnetic fields, inductor systems, circular solenoid, massive conductorAbstract
Introduction. Inductor systems, as tools for metal processing, widely used in industrial technologies using the energy of powerful pulsed electromagnetic fields. Problem. A common disadvantage of the known works on the creation of tools for magnetic-pulse impact on conductive objects has the use of physical and mathematical models, in which the exciting currents do not depend on the ongoing electromagnetic processes. Such the assumption, have distorts the picture of the real energy in the working area of the inductor system. Goal. To obtain design ratios and numerical estimates of the mutual influence of exciting and induced currents of a flat inductor system with a circular solenoid located between massive well-conducting objects, moreover to carry out a theoretical analysis of electromagnetic processes in this system. Methodology. Have applied integrating Maxwell’s equations using the Laplace and Fourier-Bessel integral transformations in the approximation of the ideal conductivity of the metal objects to be processed. Results. The calculated relations for the theoretical analysis of electromagnetic processes have obtained in the high-frequency approximation. It shown that the inductance of the studied system decreases as the objects being processed approach the solenoid and increases as they move away from it. It found that for the invariability of the power indicators, of the proposed tool, a corresponding correction of the amplitude (on average up to 20 times) of the exciting current has necessary in the solenoid winding. Originality. For the first time, the tool design with a circular solenoid located between the massive metal objects has proposed for flat magnetic-pulse stamping. As a result of the theoretical analysis, the influence of electromagnetic processes on the currents flowing in the system has confirmed. Practical significance. The use of the results obtained will allow to increase the efficiency of the tool of magnetic-pulse technologies, and to reduce the energy costs for performing the specified production operations.
References
Benenson W., Harris J.W., Stöcker H., Lutz H. Handbook of Physics. Springer Nature Switzerland AG, 2002. 1190 p. doi: https://doi.org/10.1007/0-387-21632-4.
Gnatov A., Argun S. New Method of Car Body Panel External Straightening: Tools of Method. International Journal of Vehicular Technology, 2015, vol. 2015, pp. 1-7. doi: https://doi.org/10.1155/2015/192958.
Kudasov Y.B., Surdin O.M., Platonov V.V., Kozabaranov R.V., Maslov D.A., Makarov I.V., Svetlov A.S., Popov E.Y. Metal plate deformation under magnetic field pulse of complex shape. Journal of Applied Physics, 2019, vol. 126, no. 8, p. 084901. doi: https://doi.org/10.1063/1.5108823.
Du L., Li X., Xia L., Zhang X., Lai Z., Han X., Li L., Cao Q. Numerical and experimental verification of an iterative coupling method for analyzing the Lorentz-force-driven sheet metal stamping process. The International Journal of Advanced Manufacturing Technology, 2021, vol. 115, no. 7-8, pp. 2161-2173. doi: https://doi.org/10.1007/s00170-021-07268-z.
Bay F., Jeanson A.-C., Zapata J.A. Electromagnetic Forming Processes: Material Behaviour and Computational Modelling. Procedia Engineering, 2014, vol. 81, pp. 793-800. doi: https://doi.org/10.1016/j.proeng.2014.10.078.
Ouyang S., Li C., Du L., Li X., Lai Z., Peng T., Han X., Cao Q., Li L. Electromagnetic forming of aluminum alloy sheet metal utilizing a low-frequency discharge: A new method for attractive forming. Journal of Materials Processing Technology, 2021, vol. 291, p. 117001. doi: https://doi.org/10.1016/j.jmatprotec.2020.117001.
Ouyang S., Du L., Cao Q., Li L. Electromagnetic attractive forming of aluminum alloy sheets utilizing a low-frequency half-wave current. Materials and Manufacturing Processes, 2021, pp. 1-9. doi: https://doi.org/10.1080/10426914.2021.1944197.
Batygin Y.V., Chaplygin E.A. Vortical currents in flat metallic sheet. Electrical Engineering & Electromechanics, 2006, no. 5, pp. 54-59. (Rus). Available at: http://eie.khpi.edu.ua/issue/view/6513/2466 (accessed 25 June 2021).
Turenko A.N., Batygin Yu.V., Gnatov A.V. Impul'snye magnitnye polia dlia progressivnykh tekhnologii. T. 3. Teoriia i eksperiment pritiazheniia tonkostennykh metallov impul'snymi magnitnymi poliami [Pulsed magnetic fields for advanced technologies. Vol. 3. Theory and experiment of the attraction of thin-walled metals by pulsed magnetic fields]. Kharkiv, KhNAHU Publ., 2009. 240 p. (Rus).
Batygin Yu., Barbashova M., Sabokar O. Electromagnetic Metal Forming for Advanced Processing Technologies. Cham, Springer International Publ. AG., 2018. 93 p. doi: https://doi.org/10.1007/978-3-319-74570-1.
Golovashchenko S.F., Batygin Yu.V. Sheet metal blank destacker. Patent US. US2018105373-A1, 04/19/2018.
Batygin Yu.V., Chaplygin E.A., Shinderuk S.A., Strelnikova V.A. The main inventions for technologies of the magnetic-pulsed attraction of the sheet metals. A brief review. Electrical Engineering & Electromechanics, 2018, no. 3, pp. 43-52. doi: https://doi.org/10.20998/2074-272X.2018.3.06.
Kudasov Y.B., Makarov I.V., Platonov V.V., Surdin O.M., Maslov D.A., Voronov S.L., Malyshev A.Y., Korshunov A.S., Popov E.Y., Svetlov A.S. An Experimental Setup for Studying the Deformation Dynamics of Metal Samples under Pulsed Magnetic Field. Instruments and Experimental Techniques, 2019, vol. 62, no. 1, pp. 88-92. doi: https://doi.org/10.1134/s0020441219010135.
Demirchyan K.S., Neiman L.R., Korovkin N.V., Chechurin V.L. Teoreticheskie osnovy elektrotekhniki. 4 izd. T. 3 [Theoretical Foundations of Electrical Engineering, 4th ed., Vol. 3]. St. Petersburg, Peter Publ., 2006. 318 p. (Rus).
Isaev Yu., Vasilieva O. Metody rascheta elektromagnitnykh polei [Methods for calculating electromagnetic fields]. LAP Lambert Academic Publ., 2012. 172 p. (Rus).
Altenbach H., Konkin V., Lavinsky D., Morachkovsky O., Naumenko K. Verformungsanalyse elektrisch leitender metallischer Bauteile bei Magnetimpulsbearbeitung. Forschung im Ingenieurwesen, 2018, vol. 82, no. 4, pp. 371-377. (Ger). doi: https://doi.org/10.1007/s10010-018-0285-x.
Lavinskii D.V., Morachkovskii O. K. Elastoplastic Deformation of Bodies Interacting Through Contact Under the Action of Pulsed Electromagnetic Field. Strength of Materials, 2016, vol. 48, no. 6, pp. 760-767. doi: https://doi.org/10.1007/s11223-017-9822-3.
Kantorovich L. Mathematics for Natural Scientists. Fundamentals and Basics. Springer Nature Switzerland AG, 2016. 526 p. doi: https://doi.org/10.1007/978-1-4939-2785-2.
Weber H., Ulrich H. Laplace–, Fourier– und z– Transformation. Springer Nature Switzerland AG, 2012. 236 p. doi: https://doi.org/10.1007/978-3-8348-8291-2.
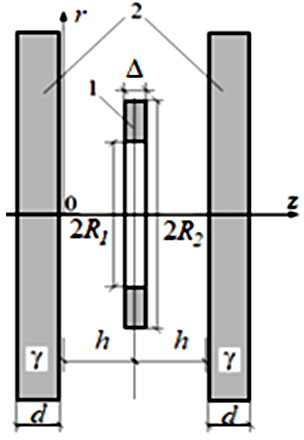
Downloads
Published
How to Cite
Issue
Section
License
Copyright (c) 2021 Yu.V. Batygin, S.O. Shinderuk, E.O. Chaplygin

This work is licensed under a Creative Commons Attribution-NonCommercial 4.0 International License.
Authors who publish with this journal agree to the following terms:
1. Authors retain copyright and grant the journal right of first publication with the work simultaneously licensed under a Creative Commons Attribution License that allows others to share the work with an acknowledgement of the work's authorship and initial publication in this journal.
2. Authors are able to enter into separate, additional contractual arrangements for the non-exclusive distribution of the journal's published version of the work (e.g., post it to an institutional repository or publish it in a book), with an acknowledgement of its initial publication in this journal.
3. Authors are permitted and encouraged to post their work online (e.g., in institutional repositories or on their website) prior to and during the submission process, as it can lead to productive exchanges, as well as earlier and greater citation of published work.