Air cavity-based vibrational piezoelectric energy harvesters
DOI:
https://doi.org/10.20998/2074-272X.2021.5.06Keywords:
piezoelectric energy harvester, air cavity, flexural membraneAbstract
Introduction. Known vibrational energy harvesting methods use a source of vibration to harvest electric energy. Piezoelectric material works as a sensing element converted mechanical energy (vibration) to electrical energy (electric field). The existing piezoelectric energy harvesting (PEHs) devices have low sensitivity, low energy conversion, and low bandwidth. The novelty of the proposed work consists of the design of PEH’s structure. Air cavity was implemented in the design where it is located under the sensing membrane to improve sensitivity. Another novelty is also consisting in the design structure where the flexural membrane was located at the top of electrodes. The third novelty is a new design structure of printed circuit board (PCB). The purpose of improvised design is to increase the stress in between the edges of PEH and increase energy conversion. With the new structure of PCB, it will work as a substrate that absorbs surrounding vibration energy and transfers it to sensing element. Methods. Three techniques were successfully designed in PEH and fabricated namely PEH A, PEH B, and PEH C were characterized by two experiments: load and vibration. The load experiment measured load pressure towards the PEH, whereas the vibration experiment measured stress towards the PEH. Results. PEH C has the highest induced voltage for a weight of 5.2 kg at the frequency of 50 Hz and the highest stored voltage for a period of 4 min. The three techniques applied in PEHs were showed improvement in transducer sensitivity and energy conversion. Practical value. A piezoelectric acoustic generator was used in the experiment to compare the performance of the designed PEH with available piezoelectric transducers in the market. The new flexible membrane worked as a sensing element was worked as a cantilever beam. PVDF was used as a sensing element due to the flexibility of the polymer material, which is expected to improve sensitivity and operating bandwidth.
References
Zhao L., Tang L., Liang J., Yang Y. Synergy of wind energy harvesting and synchronized switch harvesting interface circuit. IEEE/ASME Transactions on Mechatronics, 2017, vol. 22, no. 2, pp. 1093-1103. doi: https://doi.org/10.1109/tmech.2016.2630732.
Shekhar A., Kumaravel V.K., Klerks S., De Wit S., Venugopal P., Narayan N., Bauer P., Isabella O., Zeman M. Harvesting roadway solar energy – performance of the installed infrastructure integrated PV bike path. IEEE Journal of Photovoltaics, 2018, vol. 8, no. 4, pp. 1066-1073. doi: https://doi.org/10.1109/jphotov.2018.2820998.
Camboim M.M., Oliveira V.S., Villarim M.R., Villarim A.W.R., Catunda S.Y.C., Baiocchi O.R., De Souza C.P. An online remote verification system of thermal sources for energy harvesting application. IEEE Transactions on Instrumentation and Measurement, 2020, vol. 69, no. 10, pp. 7962-7973. doi: https://doi.org/10.1109/tim.2020.2986105.
He W., Zhang J., Yuan S., Yang A., Qu C. A three-dimensional magneto-electric vibration energy harvester based on magnetic levitation. IEEE Magnetics Letters, 2017, vol. 8, pp. 1-3, art no. 6104703. doi: https://doi.org/10.1109/lmag.2017.2669300.
Todaro M.T., Guido F., Algieri L., Mastronardi V.M., Desmaele D., Epifani G., De Vittorio M. Biocompatible, flexible, and compliant energy harvesters based on piezoelectric thin films. IEEE Transactions on Nanotechnology, 2018, vol. 17, no. 2, pp. 220-230. doi: https://doi.org/10.1109/TNANO.2017.2789300.
Khan F.U., Iqbal M. Electromagnetic bridge energy harvester utilizing bridge’s vibrations and ambient wind for wireless sensor node application. Journal of Sensors, 2018, vol. 2018, art. no. 3849683. doi: https://doi.org/10.1155/2018/3849683.
Chaudhuri D., Kundu S. MEMS piezoelectric energy harvester to power wireless sensor nodes for machine monitoring application. 2017 Devices for Integrated Circuit (DevIC), 2017, pp. 584-588. doi: https://doi.org/10.1109/devic.2017.8074018.
Shin A., Radhakrishna U., Yang Y., Zhang Q., Gu L., Riehl P., Chandrakasan A.P., Lang J.H. A MEMS magnetic-based vibration energy harvester. Journal of Physics: Conference Series, 2018, vol. 1052, p. 012082. doi: https://doi.org/10.1088/1742-6596/1052/1/012082.
Rodriguez J.C., Nico V., Punch J. A vibration energy harvester and power management solution for battery-free operation of wireless sensor nodes. Sensors, 2019, vol. 19, no. 17, p. 3776. doi: https://doi.org/10.3390/s19173776.
Correia D., Ferreira A. Energy harvesting on airport pavements: state-of-the-art. Sustainability, 2021, vol. 13, no. 11, p. 5893. doi: https://doi.org/10.3390/su13115893.
Hosseinkhani A., Younesian D., Eghbali P., Moayedizadeh A., Fassih A. Sound and vibration energy harvesting for railway applications: A review on linear and nonlinear techniques. Energy Reports, 2021, vol. 7, pp. 852-874. doi: https://doi.org/10.1016/j.egyr.2021.01.087.
Lee H., Noh M.D., Park Y. Optimal Design of Electromagnetic Energy Harvester Using Analytic Equations. IEEE Transactions on Magnetics, 2017, vol. 53, no. 11, pp. 1-5, art no. 8207605. doi: https://doi.org/10.1109/TMAG.2017.2708130.
Cai M., Liao W.-H. Design, modeling, and experiments of electromagnetic energy harvester embedded in smart watch and wristband as power source. IEEE/ASME Transactions on Mechatronics, 2021, vol. 26, no. 4, pp. 2104-2114. doi: https://doi.org/10.1109/tmech.2020.3032536.
Nabavi S., Zhang L. Nonlinear multi-mode wideband piezoelectric MEMS vibration energy harvester. IEEE Sensors Journal, 2019, vol. 19, no. 13, pp. 4837-4848. doi: https://doi.org/10.1109/jsen.2019.2904025.
Koven R., Mills M., Gale R., Aksak B. Low-frequency and broadband vibration energy harvesting using base-mounted piezoelectric transducers. IEEE Transactions on Ultrasonics, Ferroelectrics, and Frequency Control, 2017, vol. 64, no. 11, pp. 1735-1743. doi: https://doi.org/10.1109/TUFFC.2017.2739745.
Subbaramaiah R., Al-Jufout S.A., Ahmed A., Mozumdar M.M. Design of vibration-sourced piezoelectric harvester for battery-powered smart road sensor systems. IEEE Sensors Journal, 2020, vol. 20, no. 23, pp. 13940-13949. doi: https://doi.org/10.1109/JSEN.2020.3000489.
Abasian A., Tabesh A., Rezaei-Hosseinabadi N., Nezhad A.Z., Bongiorno M., Khajehoddin S.A. Vacuum-packaged piezoelectric energy harvester for powering smart grid monitoring devices. IEEE Transactions on Industrial Electronics, 2019, vol. 66, no. 6, pp. 4447-4456. doi: https://doi.org/10.1109/TIE.2018.2860557.
Nabavi S., Zhang L. Nonlinear multi-mode wideband piezoelectric MEMS vibration energy harvester. IEEE Sensors Journal, 2019, vol. 19, no. 13, pp. 4837-4848. doi: https://doi.org/10.1109/JSEN.2019.2904025.
Naval S., Sinha P.K., Das N.K., Anand A., Kundu S. Bandwidth increment of piezoelectric energy harvester using multi-beam structure. 2019 Devices for Integrated Circuit (DevIC), 2019, pp. 370-373. doi: https://doi.org/10.1109/devic.2019.8783724.
Rubes O., Hadas Z. Design and simulation of bistable piezoceramic cantilever for energy harvesting from slow swinging movement. 2018 IEEE 18th International Power Electronics and Motion Control Conference (PEMC), 2018, pp. 663-668. doi: https://doi.org/10.1109/EPEPEMC.2018.8521846.
Lu S., Boussaid F., Law M. Efficient parallel-SSHI interface circuit for piezoelectric energy harvesting. 2013 IEEE 11th International New Circuits and Systems Conference (NEWCAS), 2013, pp. 1-4. doi: https://doi.org/10.1109/NEWCAS.2013.6573658.
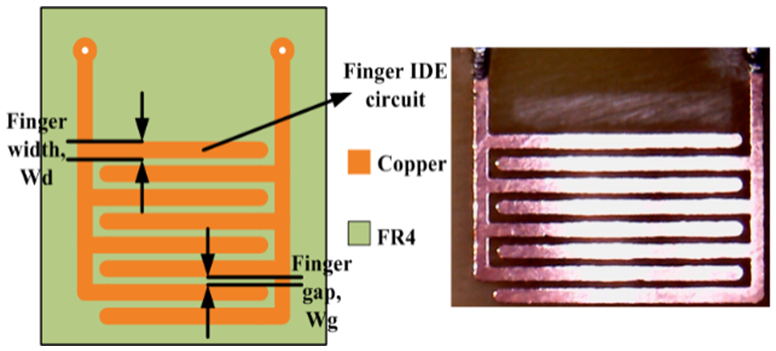
Downloads
Published
How to Cite
Issue
Section
License
Copyright (c) 2021 A. A. Mohamad Yusoff, K. A. Ahmad, S. N. Sulaiman, Z. Hussain, N. Abdullah

This work is licensed under a Creative Commons Attribution-NonCommercial 4.0 International License.
Authors who publish with this journal agree to the following terms:
1. Authors retain copyright and grant the journal right of first publication with the work simultaneously licensed under a Creative Commons Attribution License that allows others to share the work with an acknowledgement of the work's authorship and initial publication in this journal.
2. Authors are able to enter into separate, additional contractual arrangements for the non-exclusive distribution of the journal's published version of the work (e.g., post it to an institutional repository or publish it in a book), with an acknowledgement of its initial publication in this journal.
3. Authors are permitted and encouraged to post their work online (e.g., in institutional repositories or on their website) prior to and during the submission process, as it can lead to productive exchanges, as well as earlier and greater citation of published work.